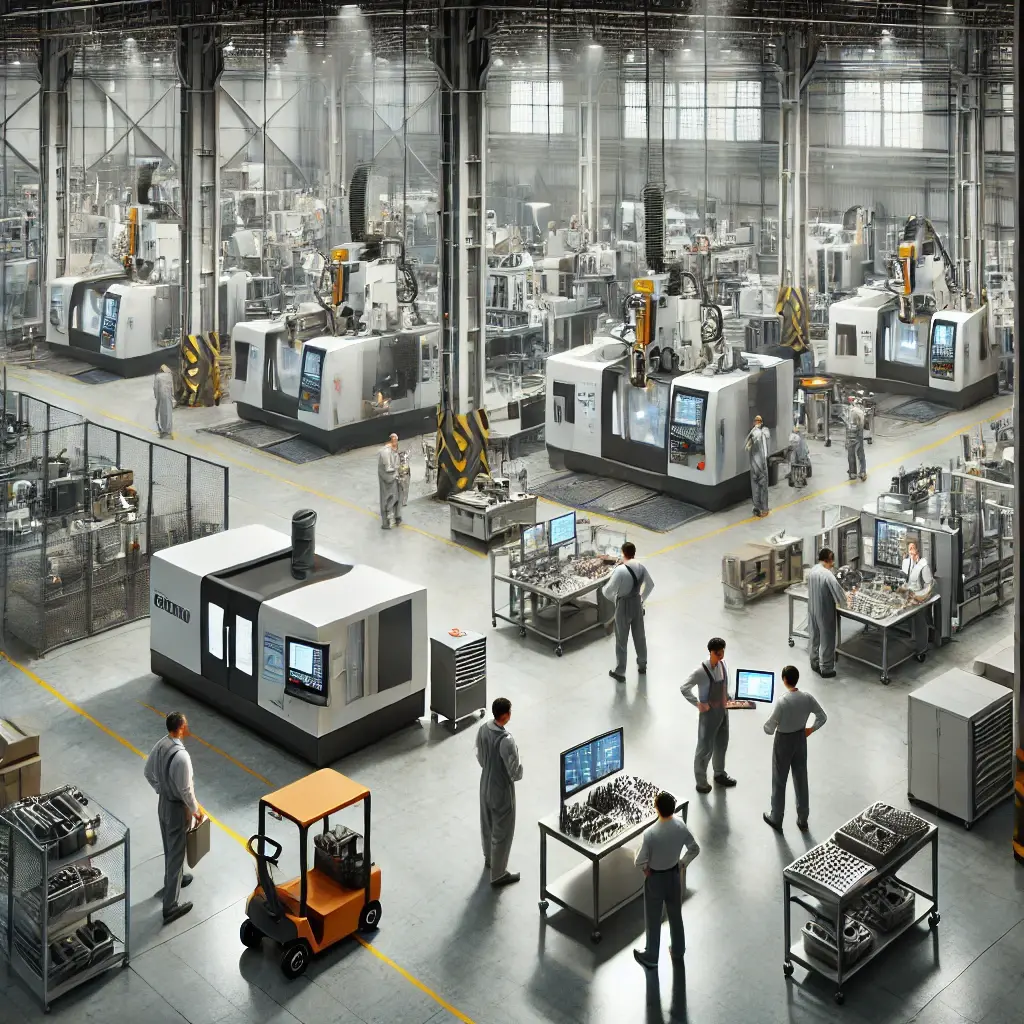
Stratégies pour Réduire les Coûts de Production en Fabrication
Introduction
La réduction des coûts de production est un objectif central pour les entreprises manufacturières cherchant à améliorer leur rentabilité tout en maintenant la qualité et la compétitivité. Chaque poste de dépense, de l’achat des matières premières à l’utilisation des machines-outils, doit être optimisé pour minimiser les pertes et maximiser la productivité.
L’efficacité passe par une meilleure planification de la production, une gestion rigoureuse des temps de cycle, et l’intégration de solutions d’automatisation et de suivi en temps réel.
Dans cet article, nous explorons sept stratégies éprouvées pour réduire les coûts de fabrication sans sacrifier la qualité ni la performance.
Optimiser la Gestion des Matières Premières
Les matières premières représentent une part importante des coûts de fabrication. Pour les réduire, il est essentiel d’optimiser la gestion des stocks et les approvisionnements.
L’utilisation d’un logiciel de planification de la production permet d’anticiper les besoins, d’éviter le gaspillage et de limiter les stocks excédentaires qui immobilisent du capital.
Le recours à des fournisseurs alternatifs, la négociation de contrats long terme et l’utilisation de matériaux plus économiques (sans compromis sur la qualité) sont des leviers clés.
Certaines entreprises adoptent aussi des stratégies de recyclage et de réutilisation des matières pour limiter les coûts et réduire leur impact environnemental.
Améliorer l’Efficacité Globale des Équipements (OEE)
Le Taux de Rendement Synthétique (TRS) est un indicateur clé pour mesurer la productivité des machines-outils et identifier les sources de perte.
Un logiciel de surveillance des machines permet d’avoir une vision en temps réel de la disponibilité, de la performance et de la qualité de la production.
Un TRS faible révèle souvent trop de temps d'arrêt, une sous-utilisation des équipements ou un taux de défauts élevé.
Pour l’améliorer, il est indispensable d’optimiser les processus, d’adopter une maintenance préventive et de réduire les arrêts non planifiés.
Automatiser et Numériser les Processus
L’automatisation est un levier majeur pour réduire les coûts de main-d'œuvre et augmenter la cadence de production.
L’intégration de robots industriels, de machines-outils numériques et de programmes CN optimisés réduit les erreurs humaines et augmente la précision.
De plus, des logiciels de planification du personnel facilitent la gestion des effectifs en ajustant les ressources en fonction de la charge de production.
La planification en direct permet de s’adapter en temps réel aux variations de la demande.
Réduire les Déchets et Améliorer la Qualité
Chaque défaut de fabrication coûte cher.
Mettre en place un programme de suivi en temps réel et appliquer des méthodes comme Six Sigma permet d’identifier rapidement les anomalies et de limiter les pertes.
Un contrôle qualité renforcé et l’adoption du flux tiré (Just-in-Time) réduisent les stocks intermédiaires et améliorent l'efficacité globale.
L'objectif est clair : produire sans gaspillage tout en garantissant la qualité.
Optimiser la Consommation d’Énergie
L’énergie est un poste de dépense important.
Pour la réduire, il faut optimiser les cycles de production, utiliser des capteurs intelligents pour ajuster la consommation, et investir dans des équipements basse consommation.
Le suivi énergétique en temps réel aide à détecter les anomalies et à cibler les équipements énergivores.
Des actions simples comme l’éclairage LED ou la récupération de chaleur peuvent générer des économies importantes.
Réduire les Temps de Changement
Les changements de série sont une source fréquente de perte.
Appliquer la méthode SMED (Single-Minute Exchange of Die) permet de réduire les temps de changement en standardisant et simplifiant les procédures.
L’utilisation d’un logiciel de suivi des arrêts facilite l’analyse des interruptions et aide à optimiser les transitions entre séries.
Former les opérateurs et automatiser certaines étapes fluidifie la production et maximise le temps de machine disponible.
Optimiser la Gestion de la Main-d’Œuvre
Une planification efficace des effectifs est essentielle pour limiter les surcoûts liés aux heures supplémentaires ou aux sous-occupations.
Les logiciels de planification du personnel permettent une répartition intelligente des tâches en fonction des compétences et des priorités de production.
La formation continue et un environnement de travail collaboratif renforcent aussi la productivité et l'engagement des équipes.
Conclusion
Réduire les coûts de production ne signifie pas baisser la qualité ni sacrifier la performance.
En combinant optimisation des matières premières, automatisation des processus, amélioration du TRS et planification dynamique des effectifs, les entreprises peuvent augmenter leur rentabilité tout en maintenant un haut niveau d'excellence opérationnelle.
L’adoption de logiciels de surveillance des machines, de systèmes de suivi des arrêts et d’outils de planification avancée permet de rationaliser les opérations et d’améliorer la flexibilité.
En appliquant ces sept stratégies, les fabricants peuvent construire des bases solides pour affronter un marché de plus en plus concurrentiel.