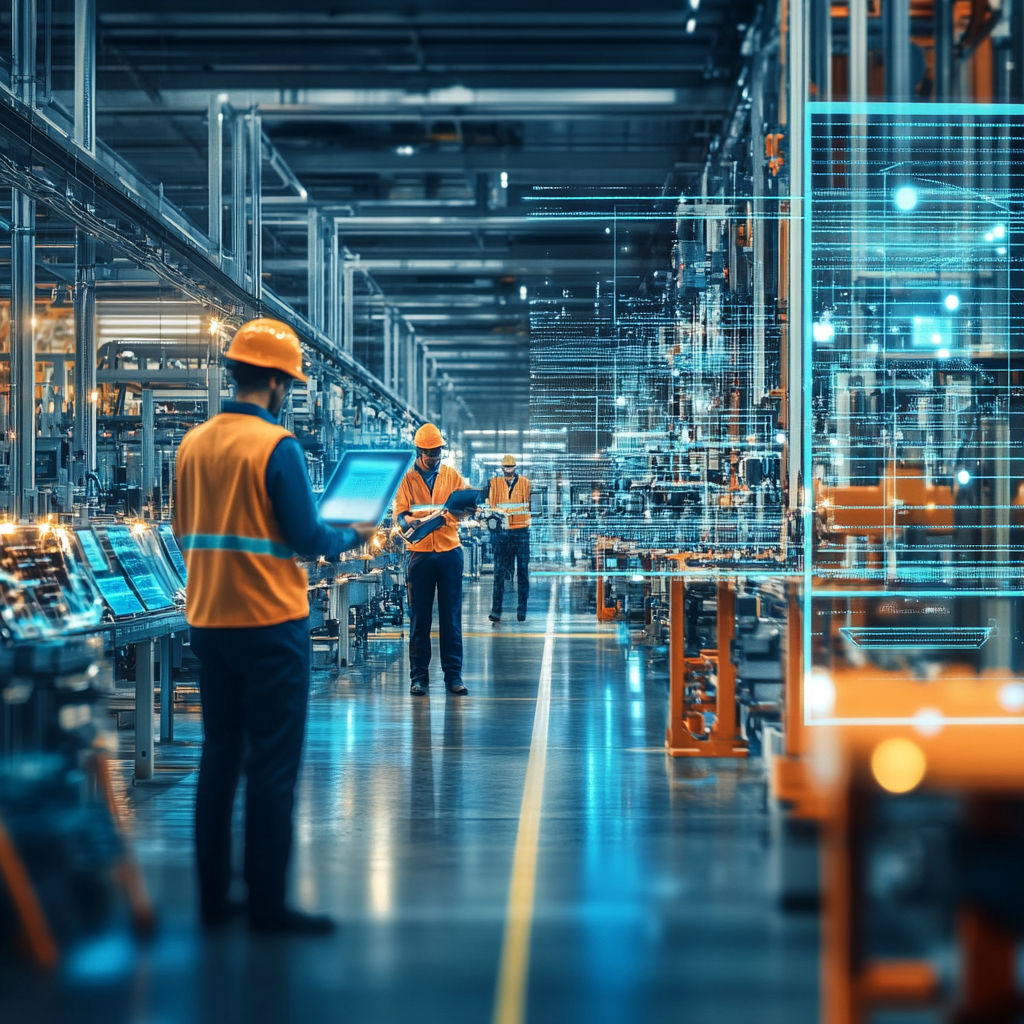
Reducing Changeover Time in Manufacturing: Key to Efficiency
Introduction
In the manufacturing industry, optimizing production processes reduces costs, minimizes downtime, and maximizes productivity. Changeover time — the period required to switch from one production run to another — is a key factor. Inefficient changeovers lead to extended downtimes, lower Overall Equipment Effectiveness (OEE), and increased labor costs.
Reducing changeover time is a cornerstone of lean manufacturing. Optimizing machine setup times and production flows improves efficiency and performance tracking.
Understanding the Impact of Changeover Time
Changeover time includes tool removal and installation, equipment calibration, and quality checks. In industries with varied and low-volume production, frequent changeovers are necessary. If not optimized, they slow down production.
OEE is a key indicator for measuring changeover efficiency. A high OEE means fewer stops and better machine utilization. Reducing changeover time directly improves this metric by increasing productive time.
SMED Method (Single-Minute Exchange of Die)
The SMED method, developed by Shigeo Shingo, aims to reduce changeover time to under 10 minutes. It is based on four steps:
- Separate internal and external tasks: Internal tasks require the machine to stop (tool changes), while external tasks can be done in advance (tool preparation). Shifting as many tasks as possible from internal to external reduces machine downtime.
- Standardize and optimize internal tasks: Using quick-change tooling, pre-configured devices, and modular systems reduces setup time.
- Eliminate unnecessary tasks: Analyze the process to remove non-value-added tasks.
- Continuous improvement: Regularly refine procedures to increase efficiency.
Implementing SMED drastically reduces setup times, improves machine usage, and optimizes labor costs.
Using Digital Tools and Automation
Technology simplifies changeovers by reducing manual interventions. Machine monitoring solutions, labor management systems, and connected devices allow real-time tracking and fast configuration adjustments.
Key tools include:
- Production tracking: Real-time performance analysis to detect inefficiencies and avoid delays.
- Automatic tool change systems: Used in CNC machines and industrial robots, they reduce human intervention.
- Digital work instructions: Interactive digital instructions reduce errors and standardize changeovers. In some use cases, this can include augmented reality.
- Advanced planning and smart scheduling: Organizing production sequences to limit unnecessary changeovers.
Integrating these technologies enhances changeover speed and precision while reducing errors.
Lean Manufacturing and Continuous Improvement
Lean manufacturing aims to eliminate waste and optimize efficiency. When applied to changeover time, certain best practices help reduce time loss.
- Eliminate waste and optimize flow
- Avoid unnecessary movement by placing required tools and parts nearby.
- Minimize trial-and-error by documenting optimal parameters and ensuring proper pre-setup.
- Use standardized checklists to streamline and speed up the process.
- Avoid unnecessary movement by placing required tools and parts nearby.
- Train and empower teams
- Train operators on best practices for quick changeovers.
- Set up a continuous improvement (Kaizen) system to collect and apply employee suggestions.
- Conduct simulations and rehearsals to help teams work efficiently under time constraints.
- Train operators on best practices for quick changeovers.
- Standardize and reduce tool and component variety
- Reduce the number of part references and use standardized tools and components.
- Work with pre-configured setups to avoid long and complex adjustments.
- Reduce the number of part references and use standardized tools and components.
By applying these best practices, you can significantly reduce production changeover times, improve overall equipment effectiveness (OEE), and increase shop floor flexibility.
Conclusion
Reducing changeover time improves efficiency and competitiveness. Applying SMED, using digital tools, standardizing procedures, and adopting lean principles minimizes downtime and optimizes production.
Technological advancements (IoT, automation, real-time monitoring) continue to transform changeovers in manufacturing. Companies that invest in these strategies improve their OEE, reduce labor costs, and gain the flexibility needed to meet market demands.
Reducing changeover time is a strategic lever to produce more efficiently, eliminate waste, and stay competitive in an ever-evolving industrial landscape.
Optimize your machine performance and maximize your productivity with our real-time monitoring platform.