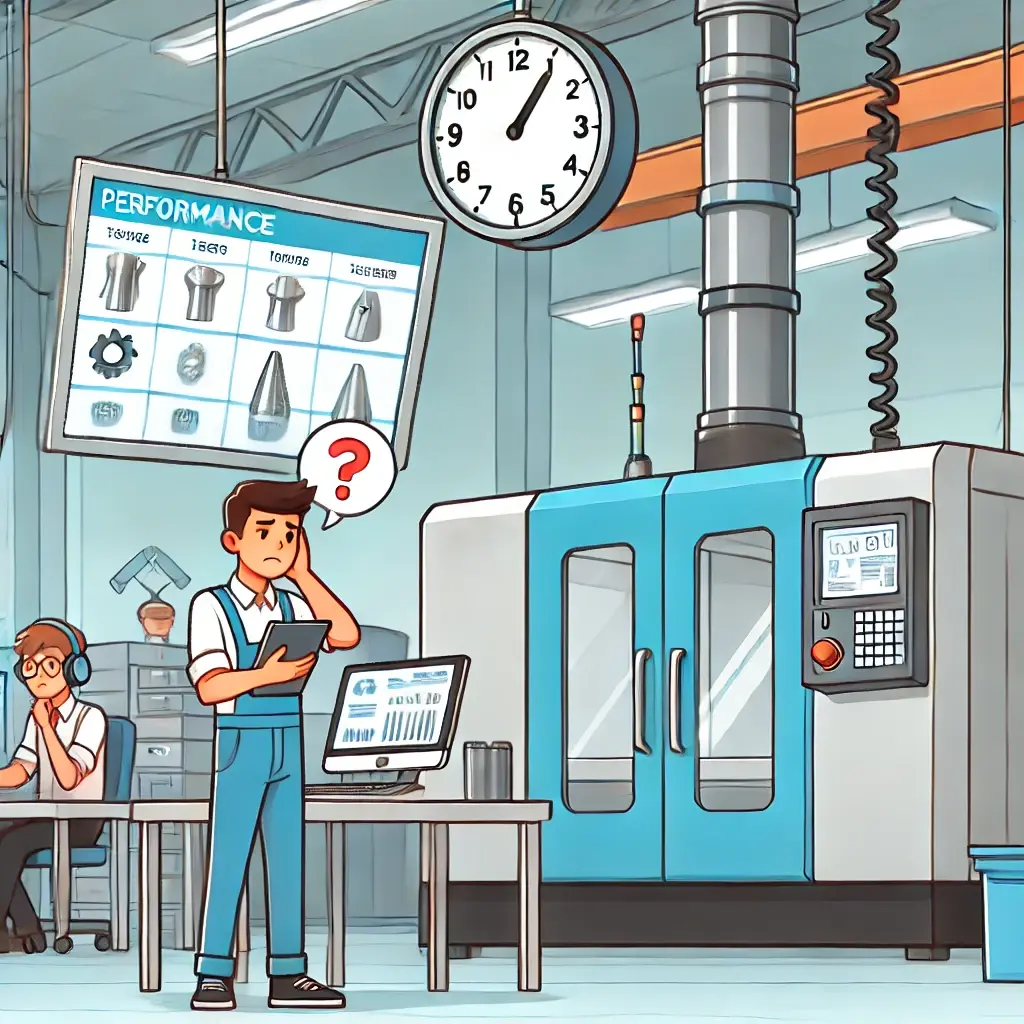
Cycle Time Reduction: Optimizing Manufacturing Efficiency
Introduction
In manufacturing, efficiency is a key factor for competitiveness and profitability. One of the most critical performance indicators is cycle time, which is the amount of time it takes to produce a product from start to finish. Poor cycle time management can lead to delivery delays, a decrease in OEE (Overall Equipment Effectiveness), and general equipment inefficiency.
Optimizing cycle time is essential to improve production planning, ensure better task allocation, and enable more effective downtime tracking. This article explores strategies to reduce cycle time using modern tools such as automated machine monitoring systems, process automation, and workforce planning software.
Understanding Cycle Time and Its Importance
Cycle time is the total time required to produce one unit, from receiving raw materials to delivering the finished product. It differs from Takt Time, which is the rate at which a product needs to be produced to meet demand, and Lead Time, which includes the full time from order to delivery.
Optimizing cycle time directly impacts equipment efficiency, delivery timelines, and production capacity. A longer-than-expected cycle time leads to reduced productivity and increased operational costs.
Factors Influencing Cycle Time
Several elements directly affect manufacturing cycle time. Real-time equipment monitoring helps identify and optimize these bottlenecks.
- Bottlenecks: When specific machines or workstations take more time than others, they slow down the entire production flow. Production data analysis helps identify these critical bottlenecks and adjust operations planning accordingly.
- Changeover time: Inefficient transitions between production batches increase cycle time. Applying the SMED (Single-Minute Exchange of Die) method helps shorten these transitions by standardizing changeover processes.
- Unplanned downtimes: Downtime tracking allows for anticipating failures and optimizing preventive maintenance, reducing unexpected stoppages.
- Workforce management: Workforce planning software ensures better task distribution and minimizes delays caused by shift changes or unbalanced workloads among operators.
- Inventory and raw material management: Poor supply coordination can slow production and increase Lead Time. Using an MRP system helps control production flows and prevent disruptions.
Strategies to Reduce Cycle Time
Cycle time optimization relies on a combination of process improvement, automation, and smarter production planning.
Process Improvement and Lean Manufacturing
Lean Manufacturing aims to eliminate waste and increase production efficiency. A key approach is Just-In-Time (JIT) production, which involves making only what’s needed, when it’s needed—reducing overproduction and storage costs.
Kaizen and Kaizen Blitz events are also powerful tools for continuous process improvement, allowing teams to collaboratively identify inefficiencies and quickly implement solutions.
Process Automation and Digitization
Adopting advanced automation technologies can significantly reduce cycle time. Integrating industrial robots, machine tools, and systems like visual recognition robotics accelerates processes and reduces human error.
Machine monitoring systems and real-time tracking solutions instantly identify bottlenecks and allow production schedules to be adjusted on the fly. Production scheduling software helps companies optimize resource management and responsiveness. Some tools, like JITbase, offer dynamic scheduling that automatically updates based on machine data, allowing for faster decision-making.
Optimizing Changeover Time and Preventive Maintenance
Effective changeover time management is key to reducing total cycle time. Implementing SMED can reduce downtime from hours to minutes during product changes.
Real-time data-driven preventive maintenance also helps anticipate breakdowns and avoid unplanned downtime that extends cycle time. Downtime and work time tracking tools are essential in this optimization.
Case Study: Cycle Time Reduction in a Manufacturing Plant
Consider a company specializing in electronic components. Before optimization, their average cycle time was 120 seconds per unit—slowing production and increasing delivery times. After a detailed process analysis, automation implementation, and integration of dynamic scheduling with JITbase, the company reduced its cycle time to 90 seconds per unit.
Key improvements included optimizing the CNC program, which led to a 30% reduction in machining time, and automating part loading/unloading with a robotic arm. As a result, the company increased its OEE by 15% and cut production costs by 10%.
Conclusion
Reducing cycle time is a powerful lever to enhance industrial efficiency and lower production costs. By integrating methods like Lean Manufacturing, automation, and live scheduling, manufacturers can reduce waste and improve their OEE.
Using MRP, MES, and dynamic scheduling software enables more accurate resource and deadline management. Implementing these strategies allows companies to significantly reduce cycle times and boost competitiveness in the global market.