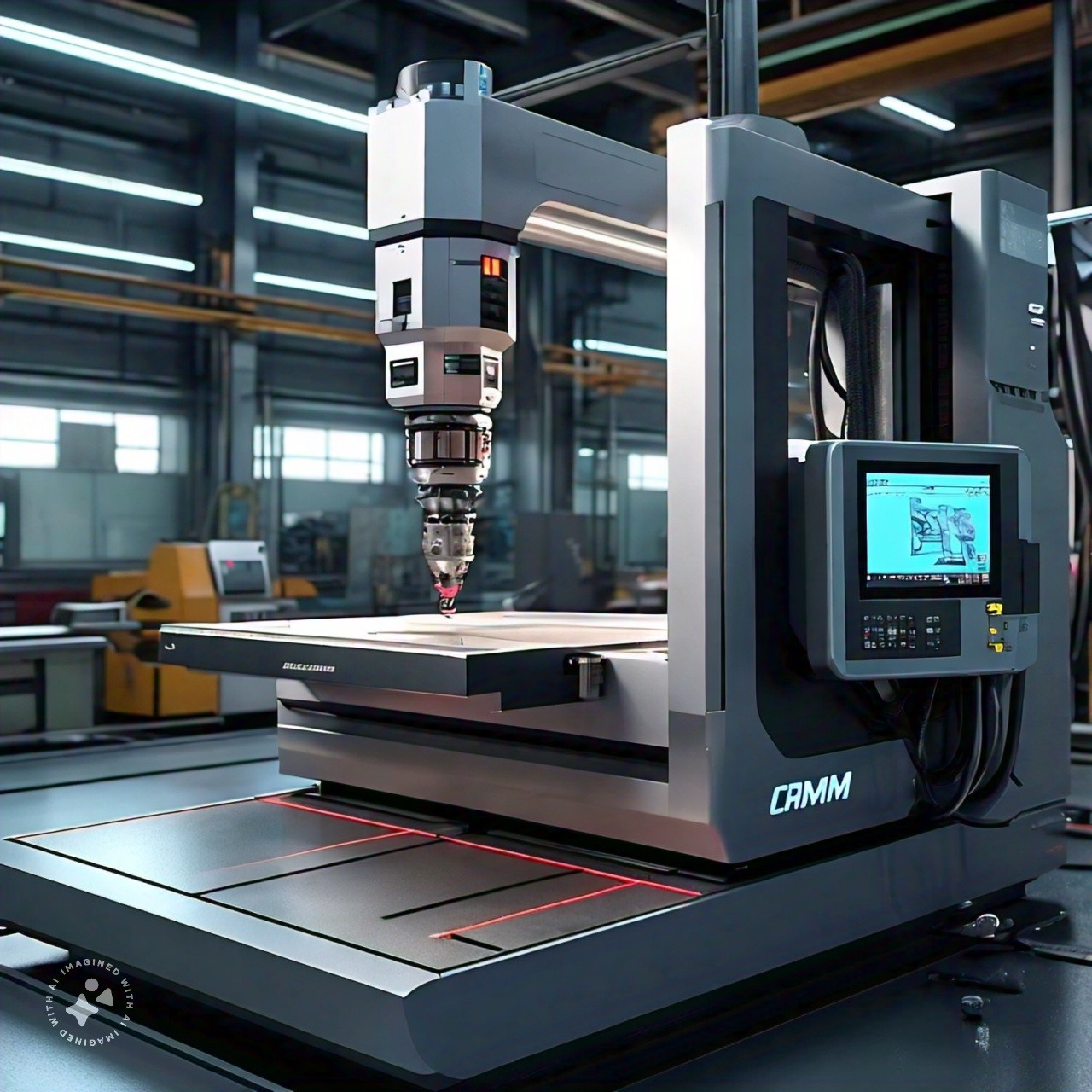
Enhancing Workflow Efficiency by Connecting Your CMM Machines with JITbase
Key Takeaways:
- Integration of CMM machines with the JITbase system is now possible
- Monitoring CMM machine utilization helps identify if inspections are causing bottlenecks, and whether there's a need for additional machines
- JITbase offers enhanced features for CMM machines, including real-time inspection tracking for operators, an inspection dashboard for upcoming inspections, and detailed analytics on first-off article and first-off inspection
In the fast-paced world of manufacturing, efficiency and precision are paramount. As technology advances, so do the tools and systems that support manufacturing processes. One such innovation is the integration of Coordinate Measuring Machines (CMMs) into a connected network. Connecting your CMMs can revolutionize your workflow, providing numerous benefits that can lead to improved productivity, accuracy, and overall operational efficiency (OOE).
Understanding CMM Machines
Coordinate Measuring Machines (CMMs) are essential tools in manufacturing for quality control and assurance. They measure the physical geometrical characteristics of an object, ensuring that parts meet design specifications. Traditional standalone CMMs, while effective, can create bottlenecks and inefficiencies within a manufacturing process. However, by connecting these machines into a networked system, manufacturers can unlock a new level of workflow optimization.
Communication protocols depend on the machine manufacturer, but as with CNC machines, MTConnect is the most common protocol.
Benefits of Connecting CMM Machines
1. Monitoring Up-Time and Usage Rates
One of the main benefits of connecting CMMs is the ability to access usage data. The data collected makes it possible to know when the machine was active or inactive and thus calculate a utilization rate.
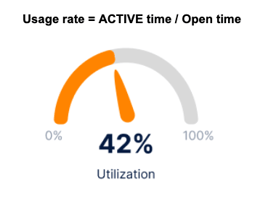
The utilization rate allows you to understand whether your machines are overused or not. If this is the case, inspection will become a bottleneck in your production flow, which is something you want to avoid. It will therefore be necessary to invest in new CMM machines.
The overall utilization rate of your CMMs is therefore an easy-to-follow performance indicator that allows you (1) to understand whether or not inspection is a bottleneck in your production workflow and (2) whether you need to invest in new equipment.
2. Real-time Inspection Tracking and Improved Collaboration Between Inspection and Production
Connecting your CMMs allows you to monitor the CMM programs running on the machines in real time and thus monitor the progress of the first article inspection.
During first article inspection (also known as FAI), the production CNC machine, and its operator, are typically waiting for the results of the first article inspection. If the first item meets tolerances the operator in charge of the machine can start production.
Thanks automatic data collection on the CMM, a production management system like JITbase can monitor the progress of the inspection in real time and confirm the completion of the inspection process directly to the operator who is working at the same time on other machines.
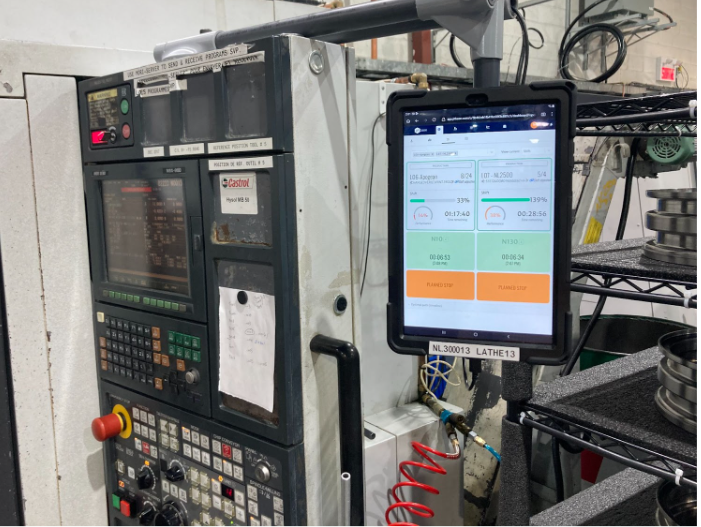
If a standard time is entered for the inspection (standard time which can be precisely analyzed thanks to the history of the data collected), the operator has continuous visibility of the time remaining to complete the inspection.
Thus the operator is much more proactive, and above all he knows, in real time, when he can start production, without having to go back and forth to the inspection department.
3. Dashboard for the Inspection Department To Reduce Delays
Thanks to the connectivity of CNC Machines, it is possible via JITbase to follow the progress of the production of the first article.
The arrival of parts for inspection can often be unpredictable. Sometimes, due to bad luck, several parts arrive at the same time and the number of inspection machines is not sufficient to launch all the inspections simultaneously. This creates a bottleneck, causing delays and down-stream delays for the CNC machines.
By following the progress of the production of the first article in real time, it is possible to predict when it will be completed and therefore subsequently arrive for inspection.
Thus, the inspection department will be able to plan the work to be carried out during the day, plan the number of inspectors needed and when, prioritize if necessary, etc.
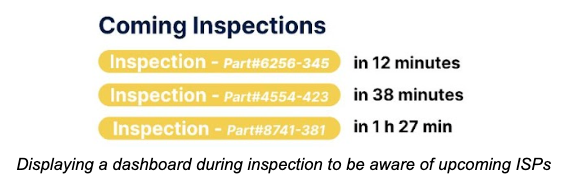
For some machinists, the CMM machines are on the floor and directly operated by the CNC operators. Likewise, a dashboard displayed on a large TV screen allows all operators to understand, at a glance, the inspections in progress, with the estimated time remaining and as well as the upcoming inspections.
4. Complete Analysis of the Machining Process
Connecting your CMMs allows you to collect machining process times, from the first article to the end of production.
Complete process of machining production:
- Setup
- First article: the data collected on the CNC machine allows us to know when the first article is launched, ending the adjustment; then when the first article is completed
- Waiting for inspection
- FAI (First Article Inspection): the data collected on the CMM machine allows us to know when the FAI begins, which allows us to know how long the article was waiting since the end of machining; then when the FAI is completed.
- Waiting for production
- Production: the data collected on the CNC machine allows us to know when production (i.e. the 2nd part if the FAI is good) is started, which allows us to know how much time has passed between the end of the FAI and the start of production.
Subsequently, the data collected on the CNC machine makes it possible to know the cycle times of each part produced.
These analyzes not only make it possible to understand where the process can be improved and if there are delays in the flow, but also to collect precise standard times for each key step in the process.
5. Streamlined Workflow Integration
Monitoring each step of the machining process in real time, from setup to production, including FAI, allows operations to be better planned and adjusted as needed.
JITbase offers a ‘live’ planning solution which allows you to visualize the progress of the different stages of the production process at all times. It is therefore possible to see the expected end date and time of a production order (PO) which is readjusted according to the actual progress in production. This precision makes it possible to better understand the delays if there are any, to adapt the plan if necessary and to understand when a certain machine will be available for a next operation.
Implementing a Connected CMM Network
Transitioning to a connected CMM network requires careful planning and execution. Here are some steps to consider:
- Assess Current Infrastructure: Modern CMM machines can be plugged into your internal network via an Ethernet cable. Depending on the machine brands, a communication protocol will be available or must be installed on the machine to generate data. The standard communication protocols for CMM machines are MTConnect and OPC-UA. If in doubt, contact your machine and question representative.
- Connecting your CMM machines to your network: Make the Ethernet wire connection to make them available on your internal network. Configure a fixed IP address for the machine and validate the port to access the communication protocol.
- Adding machines to JITbase: With the correct communication protocol installed, JITbase is able to instantly capture data from your CMM machines accessible on your internal network. Simply add the IP address and port of your CMM machine into your JITbase environment… and voilà!
Don’t hesitate to try: we offer free machine connectivity for up to 5 machines!