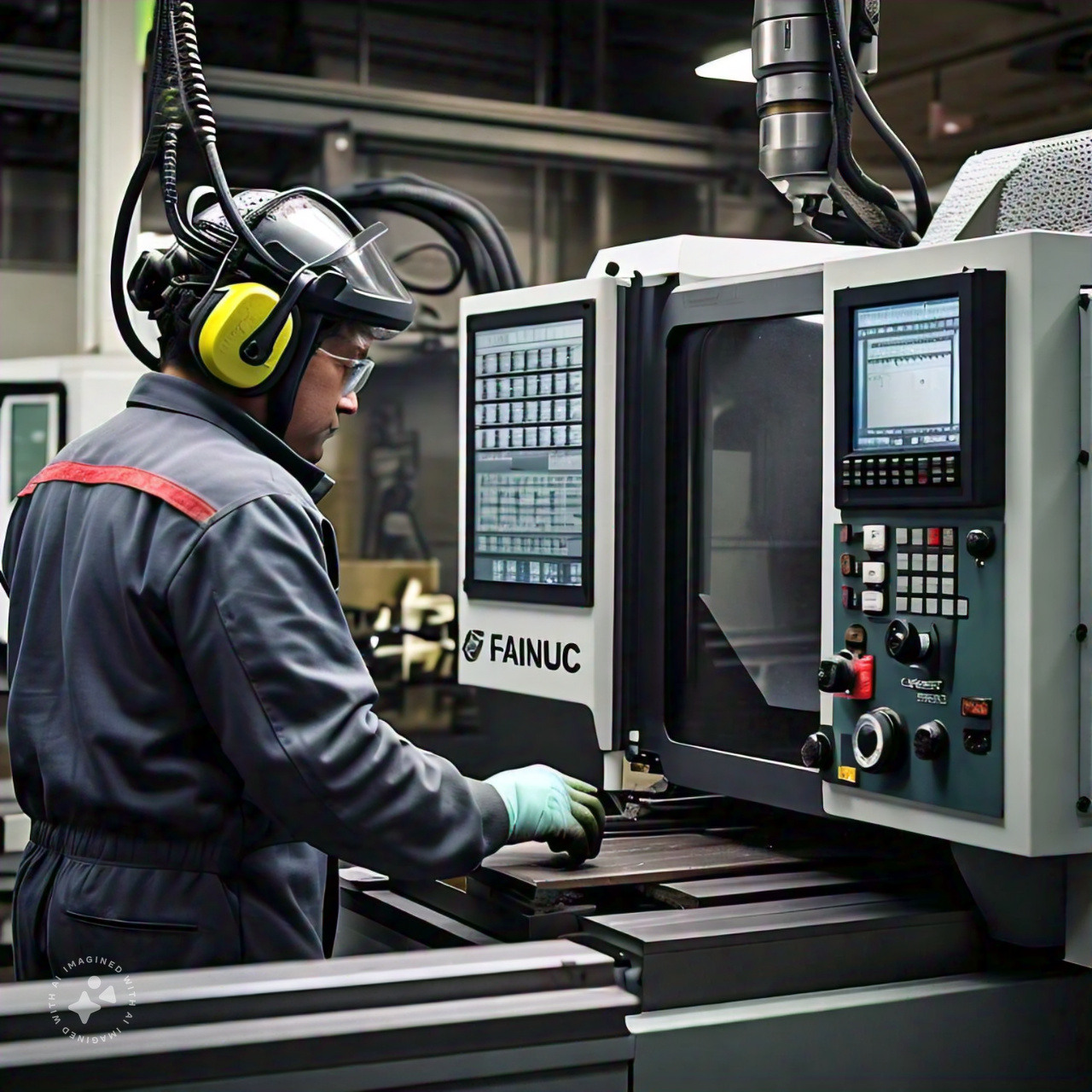
How do JITbase’s Planning & Scheduling tools complement MRP and MES systems?
Key takeaways
- ERP, MRP and MES systems are good for mid-to-long term planning, but JITbase provides the granularity and tools for daily planning
- Because it is based on machining time, manual tasks, and shifts, JITbase’s job completion estimates are more accurate than an MRP and an MES
- JITbase also calculates the machinist's workload to better balance out the task assignments
Planning is the lifeblood of manufacturing; without a proper plan your products are not produced and shipped on-time, and you risk becoming an unreliable link in your client’s supply chain. Without a proper plan, the raw materials and tools you require are not in stock and production delays will have a knock-on effect throughout your shop.
To ensure schedules are respected we have ERP and MRP systems: tools that take into account your medium and long-term planning needs. From raw materials procurement to planning and prioritizing parts to be produced.
The limitation of MRP and MES for daily scheduling
There is one element, however, that modern MRP systems do not take into consideration in sufficient granularity for daily scheduling, even coupled with MES systems: the human element. Although MRP and MES systems do include the human element, these systems are not designed to monitor manual tasks during the production process.
In fact, in CNC machining, various tasks can be performed during the production, when machines are active: part changeovers, planned stops (M00) to remove chips, change part position, perform tool changes or quality controls, etc. Not to mention optional stops (M01) usually used during the first-off, but sometimes also activated by the operators in production…
The problem is that MRP and MES systems do not accurately take these tasks into account in the planning and scheduling process.
MRPs are great for planning and organizing work on your shop floor weeks and months in advance, however when it comes to planning daily human resource allocation and workload, the MRP does not have sufficient information to factor this into the calculation.
Enter JITbase’s Planning & Scheduling tool: a complementary tool to help supervisors bridge the gap between the MRP plan and the daily reality of operator allocation by taking the human factor into account.
Medium & Long-Term Planning in MRPs
ERP software (Enterprise Resource Planning) is a modular software that consolidates the information needed to manage your business and provides your teams with tools to operate optimally in all areas. All departments are integrated into a single system, enabling process digitization, including planning based on customer orders.
MRP software (Material Requirements Planning) allows planning capabilities that include material requirement, inventory management and procurement scheduling. It manages delivery timing and builds the production schedule to meet the demand. MRP is either a module of the ERP or a third-party system connected to the ERP.
It is often coupled with MES software (Manufacturing Execution System) to get “live” updates from the shopfloor (if the MES is connected to machines and does not only rely on operator scanning systems). MES helps to track work in progress, calculate OEE, manage resource and operator schedules.
MRP focuses on manufacturing and is designed for users in related departments. A manufacturing company uses an MRP system to manage its production plan, thus forecasting and ordering materials in appropriate quantities to arrive at the determined date.
Summary- Advantages and Limitation of MRP & MES for manufacturing Planning
Advantages
- Global coordination of resources across different business units
- Inventory management
- Procurement and supply chain management
Limitation
- Lack of granularity for daily planning
- Missing Data: Absence of details on manual interventions (part change, M00, quality checks).
- Not real-time if not directly connected to CNC machines: Plans are updated by operator scans into a clocking system often at the end of a production cycle or at the end of a shift
Consequences
- Operator workload is not precise; some operators may be performing many manual tasks throughout the day while others are standing next to a machine simply waiting for it to finish.
- Difficult to optimize the operator and machine management with lack of precise data
- No real-time visibility on the advancement of the production plan; is there a problem on the shop floor? Will the jobs be completed on time?
Short-Term Planning in JITbase
JITbase is a real-time planning and scheduling tool connected to your CNC machines. It includes labor management thanks to a layer of data on manual tasks inaccessible to MRP and MES systems. Based on your CNC programs and historical data, JITbase captures the setup, part changeover, and M00 (planned stops) of your programs and integrates this data into the planning operator allocation process.
Daily planning and scheduling
JITbase focuses on the daily planning and scheduling of jobs and operator allocation to machines with an emphasis on ensuring operators are not over or under utilised, and perhaps allocating operators to multiple machines based on the manual operations required on a machine.
While MRP software is used by planners to ensure material availability and to prioritize work orders per machine, JITbase’s daily production planning tool is used by supervisors to organize operations throughout the day in order to deliver the plan provided by the MRP.
Advantages
- Workload prediction: Thanks to the capture of manual tasks durations, JITbase is able to accurately predict the workload of operators on their assigned machines which help supervisors make better decisions on the allocation.
- Precise manual-task data that are not accessible by MRP and MES systems. Instead of tracking high-level downtime, JITbase automatically knows about the tasks that take longer than expected.
- Real-time updates: Monitoring of the progress and performance of Work Orders in real time, which allows informed decision-making and adjustments during the shift possible.
- Up-to-the-minute estimated job completion time based on the live progress of both machining and manual task duration
Integration between MES/MRPs and JITbase
JITbase does not replace your MRP system nor your MES system: it is complementary to it, helping you to better plan work and operator allocation on machines. Your MRP system will still provide you with the best priority in which to complete your work orders in order to meet your deadlines, however JITbase will help you determine if your work and resource allocation on your CNC machines is the optimal allocation, or if there will be any potential bottlenecks.
Inter-connectivity between ERP, MRP, MES, and JITbase systems
With JITbase you will be able to visualise the machining and manual tasks on multiple machines and see if they “fit” well together. You will also be able to calculate the workload of your operators for a shift, allowing you to reallocate operators with low workload to other machines thereby increasing your productivity.
By taking both the machine and human factors into account, JITbase is able to better predict the end of a production more accurately, allowing you to have more confidence in your ship dates.
Conclusion
JITbase and your MRP and MES systems work together to optimize your production planning: the MRP working on your medium and long-term plan, and JITbase on your short-term (hourly/daily) plan. By gathering data directly from the CNC machines and by interpreting data about the manual tasks performed by the operators, we capture an extra layer of information about your production capabilities that MRP and MES systems can’t access by design.
Thanks to JITbase, you are able to better allocate your operators onto your machines, get up-to-the-minute updates about the progress and performance of your production, and quickly adjust allocation and production schedule if any problems arise.
In conclusion, MRPs are used by Planners to plan work orders to execute based on demand and deadlines, while ensuring material availability; JITbase’s production schedule tool is used by Supervisors to optimally allocate jobs and operators onto machines and track the planning progress in real-time to adapt if needed.