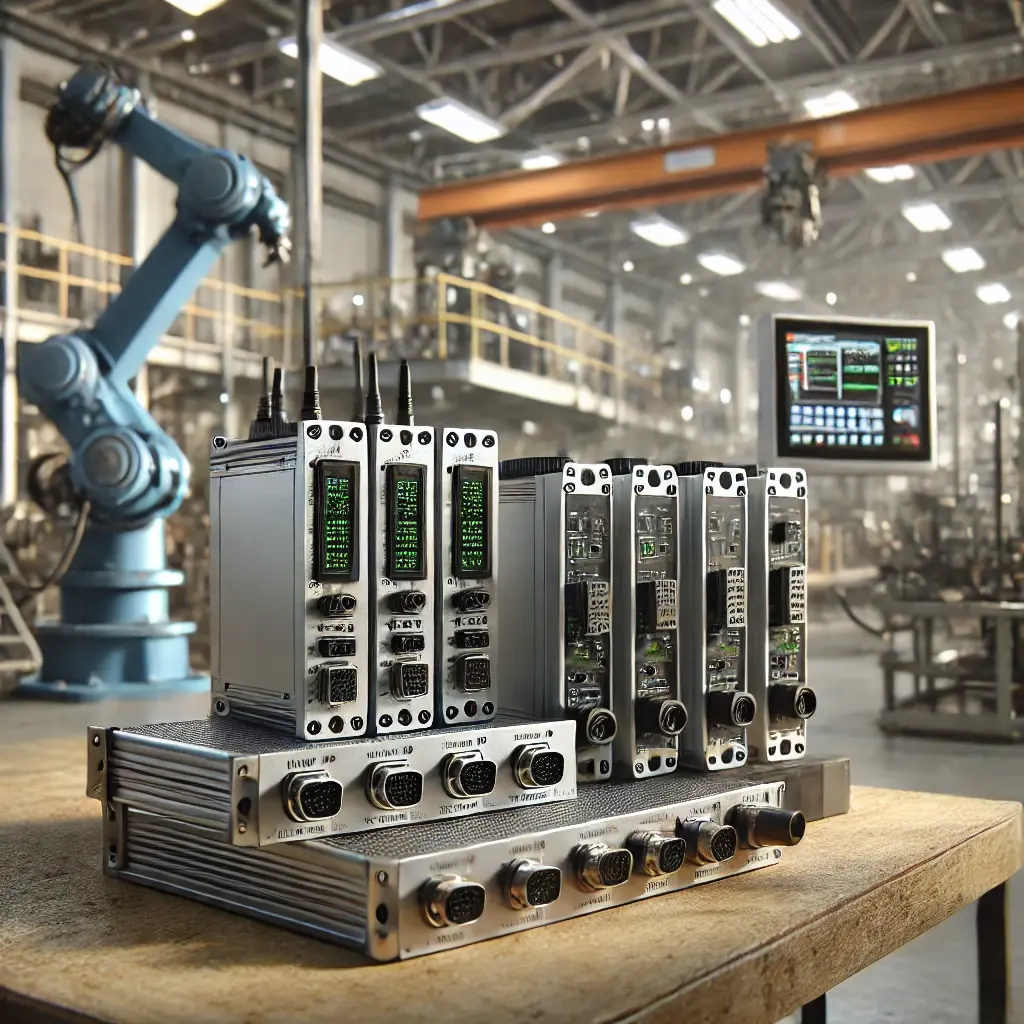
Understanding the Role of the Internet of Things in Industrial Automation
Introduction
In industrial automation, the Internet of Things (IoT) plays a critical role by enabling the interface between machines, sensors, actuators, and control systems. These modules enable machine monitoring, real-time data acquisition, and automated control, ensuring smooth operations in smart manufacturing environments. As Industry 4.0 evolves, connectivity solutions like I/O modules are essential for increasing productivity, reducing downtime, and optimizing Overall Equipment Effectiveness (OEE).
This article explores the different types of I/O modules, their applications, advantages, and how modern automation technologies integrate real-time machine data to optimize industrial processes.
What Is an I/O Module?
I/O modules act as intermediaries between a production tracking system and machines, transmitting signals that help interpret production-related information, such as machine status (Active / Inactive) or quantities produced. These modules are categorized based on the type of signals they process:
- Analog I/O modules: Handle continuous signals such as temperature, pressure, and voltage levels to make real-time adjustments.
- Digital I/O modules: Manage binary signals (0 or 1). Commonly used in the industry by probing electrical current to interpret a machine's status (ON / OFF).
- Remote I/O modules: Enable connectivity between distant sensors and centralized control systems, reducing wiring complexity in large-scale facilities.
How I/O Modules Improve Industrial Efficiency
Effective performance tracking is essential in modern manufacturing. I/O modules facilitate real-time production tracking, allowing operators to detect inefficiencies, anticipate breakdowns, and optimize production flow. When integrated with OEE tracking software, these modules help monitor and improve availability, performance, and quality.
I/O modules can also be used for predictive maintenance by continuously updating machine status. For example, vibration sensors connected to an analog I/O module can detect early signs of motor wear, helping to avoid unexpected downtime.
Centralized vs. Distributed I/O Architectures
- Centralized I/O Architecture
In traditional setups, I/O modules are grouped within a central control panel, requiring extensive wiring between sensors, actuators, and controllers. - Distributed I/O Architecture
Modern industrial automation favors distributed I/O systems, where modules are placed near the machines. This approach reduces wiring, minimizes latency, and enhances real-time data exchange using industrial Ethernet protocols like PROFINET, EtherNet/IP, and Modbus.
The Role of I/O Modules in Industry 4.0
With the rise of Industry 4.0, I/O modules are evolving to support connected manufacturing environments. Advanced production tracking solutions integrate I/O modules with cloud-based analytics, providing real-time insights such as machine performance or energy consumption tracking, tailored to the manufacturer’s needs.
Modern I/O modules also feature edge computing capabilities, allowing data processing at the source instead of relying on centralized systems. This reduces data transmission latency and improves the responsiveness of automated processes.
Key Features of Modern I/O Modules
- High-speed data processing: Enables fast communication between machines and control systems.
- Scalability and flexibility: Modular designs allow easy expansion according to manufacturing needs.
- Enhanced environmental protection: IP67-certified I/O modules resist dust, moisture, and extreme temperatures.
- Real-time diagnostics: Detect signal inconsistencies and alert operators of malfunctions.
- Cybersecurity: Modern I/O modules include encryption protocols to protect connected industrial networks from cyber threats.
Integration with Advanced Industrial Technologies
I/O modules integrate seamlessly with smart manufacturing platforms that use AI-based data analysis, cloud computing, and machine learning algorithms. This integration enables manufacturers to adopt predictive maintenance strategies, reducing downtime and improving OEE.
Moreover, augmented reality (AR) solutions are used alongside I/O modules for remote troubleshooting and operator training. For example, a technician wearing AR glasses can receive real-time diagnostics from an I/O module, facilitating decision-making and reducing intervention times.
Choosing the Right I/O Module for Your Application
When selecting an I/O module, manufacturers should consider:
- Signal type: Analog, digital, or hybrid modules depending on application needs.
- Communication protocols: Compatibility with industrial networks like PROFIBUS, CANopen, DeviceNet, or OPC-UA and MTConnect in machining environments.
- Environmental conditions: Protection certifications (IP65, IP67) for harsh industrial settings.
- Scalability: Modular options for future automation expansion.
Conclusion
I/O modules are at the heart of industrial automation, facilitating communication between control systems and machines. As smart factories adopt advanced production tracking, OEE monitoring, and predictive maintenance solutions, the demand for high-performance I/O modules continues to rise.
By integrating real-time data analytics, cloud computing, and edge computing, I/O modules enable manufacturers to boost efficiency, reduce downtime, and enhance overall operational performance. Investing in the right I/O solution ensures smooth automation, increased productivity, and long-term competitiveness in a rapidly evolving industrial landscape.
Optimize your machine performance and maximize your productivity with our real-time monitoring platform.