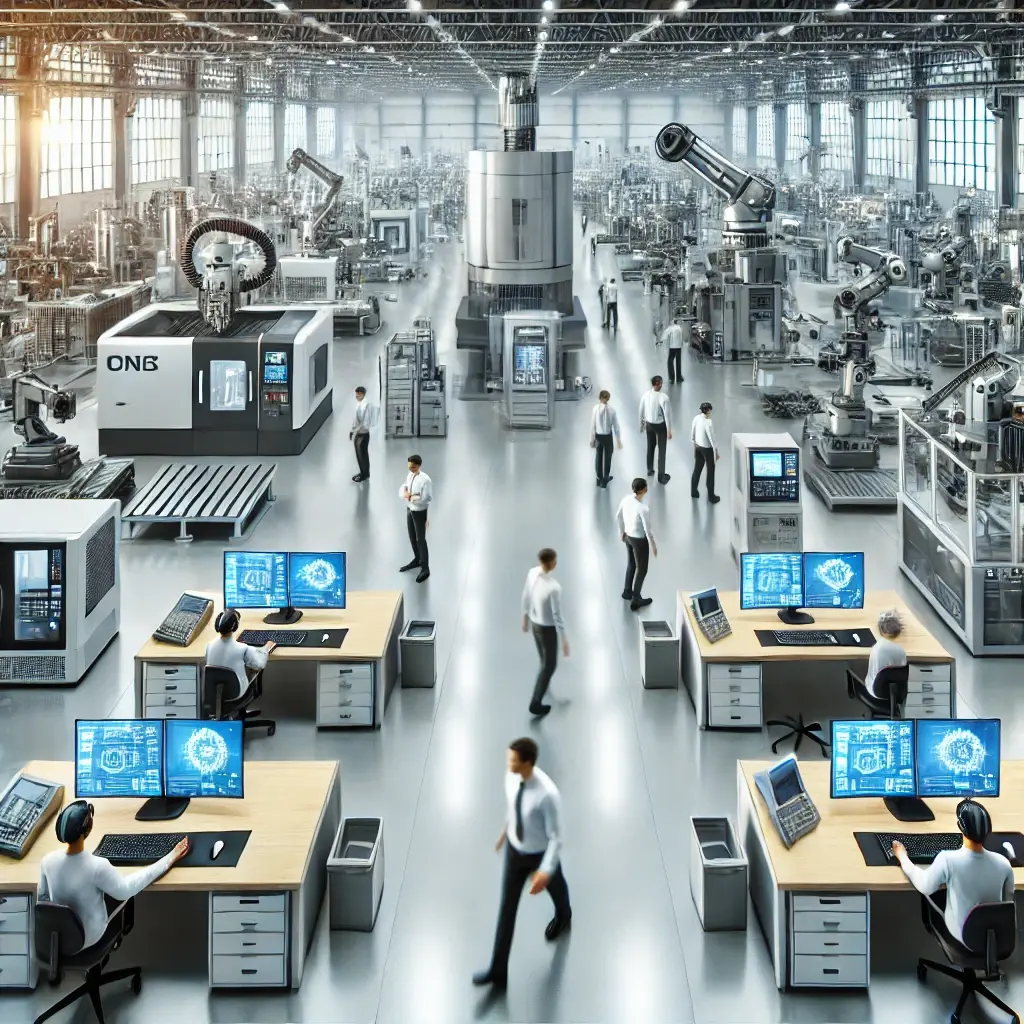
Optimizing Production with CNC Machine Monitoring Software
Introduction
Production optimization requires effective monitoring of industrial equipment. In modern workshops, CNC machine monitoring plays a crucial role in enhancing productivity, reducing downtime, and optimizing performance. Machine monitoring software enables manufacturers to collect and analyze live data, facilitating decision-making and improving Overall Equipment Effectiveness (OEE).
Implementing CNC program monitoring software helps businesses maximize equipment utilization, identify inefficiencies, and anticipate maintenance needs. This article explores the benefits of real-time CNC machine monitoring, its key functionalities, and its impact on operational efficiency.
Why CNC Machine Monitoring is Essential
CNC machines are at the heart of numerous manufacturing industries, from aerospace to automotive. However, without a performance monitoring system, companies struggle to measure productivity and reduce losses.
A primary challenge is managing downtime. Real-time monitoring quickly detects unplanned stops and identifies their causes. By analyzing this data, manufacturers can enhance production planning, adjust maintenance schedules, and optimize CNC programs for better performance.
Key Functionalities of CNC Machine Monitoring Software
CNC machine monitoring software provides several features to enhance operations management and performance optimization:
Real-Time Data Collection: Records machine performance, cycle times, downtimes, and anomalies. Productivity Analysis: Provides detailed reports on OEE, machining times, and overall equipment efficiency. Downtime Tracking: Identifies causes of interruptions and facilitates corrective actions. Preventive Maintenance Planning: Utilizes historical data to anticipate failures and avoid unexpected production stoppages. Remote Monitoring: Enables operators and managers to access machine data from any connected device.
Benefits of CNC Machine Monitoring Systems
Integrating CNC program monitoring software transforms production management, enabling a proactive rather than reactive approach. The primary benefits include:
- Improved OEE and Productivity Precise equipment efficiency hinges on availability, performance, and quality. Accurate CNC machine monitoring identifies periods of inactivity, enabling continuous improvement strategies. By reducing unplanned downtime and optimizing cycle times, manufacturers enhance OEE and maximize machine utilization.
- Reduced Downtime and Production Delays Real-time monitoring allows businesses to analyze interruptions and adjust processes to minimize time losses. Rapid problem identification lets maintenance teams intervene before significant breakdowns occur.
- CNC Program and Task Management Optimization Task planning software optimizes machining sequences and adjusts parameters based on real machine performance. Combining live scheduling with advanced analytical tools helps operators enhance efficiency and reduce waste.
Automation and Quality Improvement Modern CNC monitoring solutions integrate with advanced automation systems, reducing the need for human intervention. Increased precision minimizes manufacturing defects and improves process consistency.
Implementing CNC Monitoring Software
Deploying a CNC performance monitoring system requires a strategic approach to ensure optimal return on investment. Key steps include:
Defining Objectives and Key Indicators Before adopting a monitoring solution, clearly identify performance goals. Essential indicators include:- Overall Equipment Effectiveness (OEE)
- Machine utilization rates
- Number and duration of unplanned stops
- CNC program efficiency
- Compatibility with existing machines
- Integration with production planning software
- User-friendly interfaces and real-time data access
Training Operators and Production Managers The effectiveness of CNC monitoring software depends on its adoption by production teams. Comprehensive training ensures optimal utilization of software functionalities and effective data use.
Continuous Analysis and Improvement Regularly reviewing reports and seeking improvement opportunities are crucial after implementation. Analyzing production trends helps refine workforce planning, optimize processes, and anticipate maintenance needs.
Case Study: Enhancing Productivity with CNC Monitoring Software
Consider a precision machining company that frequently faced downtime and inefficient equipment utilization before implementing CNC monitoring software. By integrating real-time monitoring, the company:
- Reduced downtime by 30% through optimized preventive maintenance.
- Increased OEE by 15% through improved machine performance management.
- Reduced raw material waste by adjusting machining parameters based on collected data.
This transition significantly enhanced the company's competitiveness and reduced production costs.
Conclusion
Adopting CNC machine monitoring software is essential for manufacturers aiming to boost productivity, minimize downtime, and optimize operations. Real-time scheduling, downtime tracking, and CNC program optimization enable businesses to maximize their OEE and ensure smoother production.
Investing in machine monitoring solutions reduces costs, improves quality, and increases flexibility to market demands. With these tools, manufacturers achieve sustainable operational excellence and strengthen their competitive position.