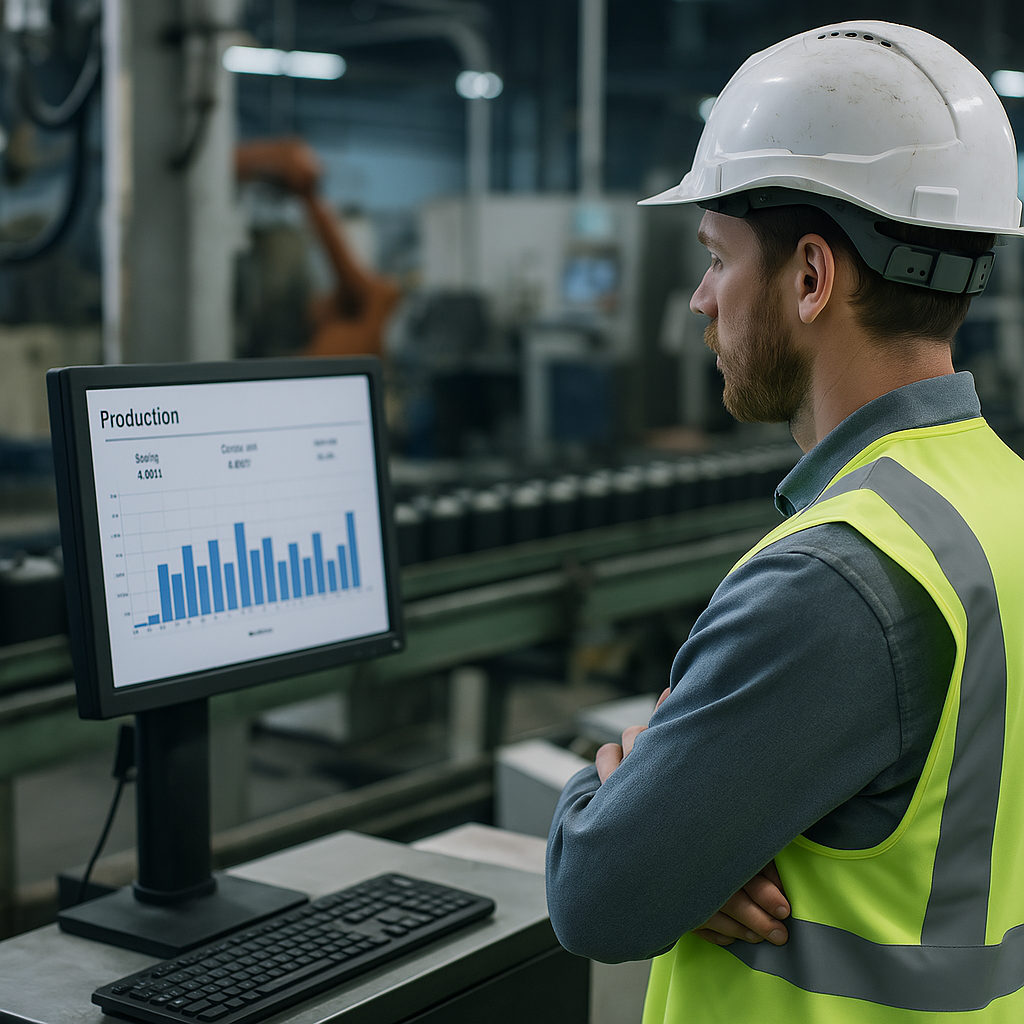
Understanding Takt Time, Cycle Time, and Lead Time in Production
Introduction
In manufacturing and process management, three core concepts are essential to optimize productivity and improve production planning: Takt Time, Cycle Time, and Lead Time. These indicators are crucial for performance tracking, managing the production schedule, and improving overall equipment effectiveness (OEE).
However, these terms are often misunderstood, leading to errors in process optimization and workforce scheduling. Mastering these concepts helps balance task allocation and enables more effective live planning.
What is Takt Time?
Takt Time represents the pace at which a product must be manufactured to meet customer demand. It is defined based on the available production time and demand, making it a key indicator in job scheduling and optimizing the production schedule.
The formula for Takt Time is simple:
Available production time / Customer demand
For example, if a company has 8 hours of production per day (28,800 seconds) and the customer demand is 200 units per day, then:
Takt Time = 28,800 / 200 = 144 seconds
This means that to meet customer demand and ensure effective program monitoring, the company must produce one unit every 144 seconds.
What is Cycle Time?
Cycle Time is the time required to produce one complete unit, from start to finish. Unlike Takt Time, which is dictated by customer demand, Cycle Time measures actual production capacity and allows for real-time performance tracking of equipment.
If Cycle Time is shorter than Takt Time, the company is producing faster than the demand, potentially leading to overproduction and resource waste. Conversely, if Cycle Time is longer than Takt Time, the company risks delivery delays and a drop in OEE, making better workforce scheduling and production planning necessary.
What is Lead Time?
Lead Time is the total time between a customer order and the delivery of the finished product. It includes multiple components such as waiting time before production starts, actual manufacturing time, and transportation time.
In an industrial context, reducing Lead Time is a key goal to improve production planning and ensure effective deadline management. Accurate tracking of cycle times and changeover times helps optimize resource management and enhance OEE.
Comparison of Takt Time, Cycle Time, and Lead Time
Concept |
Definition |
Formula |
Impact on Production |
Takt Time |
Time required to produce one unit according to customer demand |
Available production time / Customer demand |
Sets the production pace |
Cycle Time |
Actual time needed to produce one unit |
Manufacturing time per unit |
Measures real production performance |
Lead Time |
Total time from order to delivery |
Waiting + Production + Delivery |
Affects customer satisfaction and inventory management |
Optimizing Takt Time, Cycle Time, and Lead Time
A good balance between these three metrics requires process improvements and real-time machine monitoring. Implementing manufacturing scheduling software and using a labor management system allows for resource adjustment according to needs.
One of the key levers for optimization is reducing changeover times. With strategies such as SMED (Single-Minute Exchange of Die), it’s possible to minimize production interruptions and improve workflow continuity. By reducing these cycle times, the company boosts its OEE and makes better use of its machines.
Automation also plays a critical role in improving Cycle Time. The use of industrial robots and automated systems speeds up repetitive tasks and minimizes human error. Combined with effective workforce scheduling, this approach ensures a production pace better aligned with market demands.
Case Study: Application in an Automotive Parts Plant
Take the example of an automotive parts manufacturing plant. The company needs to produce one part every 60 seconds to meet market demand. However, its current Cycle Time is 75 seconds per part, leading to production delays and assembly line congestion.
By applying the SMED method and optimizing task scheduling, the company reduces its Cycle Time to 60 seconds. It also implements real-time monitoring of machine performance and adjusts its preventive maintenance program to minimize unplanned downtime. This approach allows it to align its manufacturing pace with Takt Time and reduce Lead Time from 10 days to 7 days.
Conclusion
Optimizing Takt Time, Cycle Time, and Lead Time is a strategic priority for improving industrial efficiency and ensuring smooth, high-performing production. By aligning these three metrics, a company can not only maximize its OEE but also improve workforce planning and production scheduling.
Through better task allocation, the use of scheduling software, and automation, companies can minimize downtime, reduce waste, and enhance customer satisfaction.
Optimize your machine performance and maximize your productivity with our real-time monitoring platform.