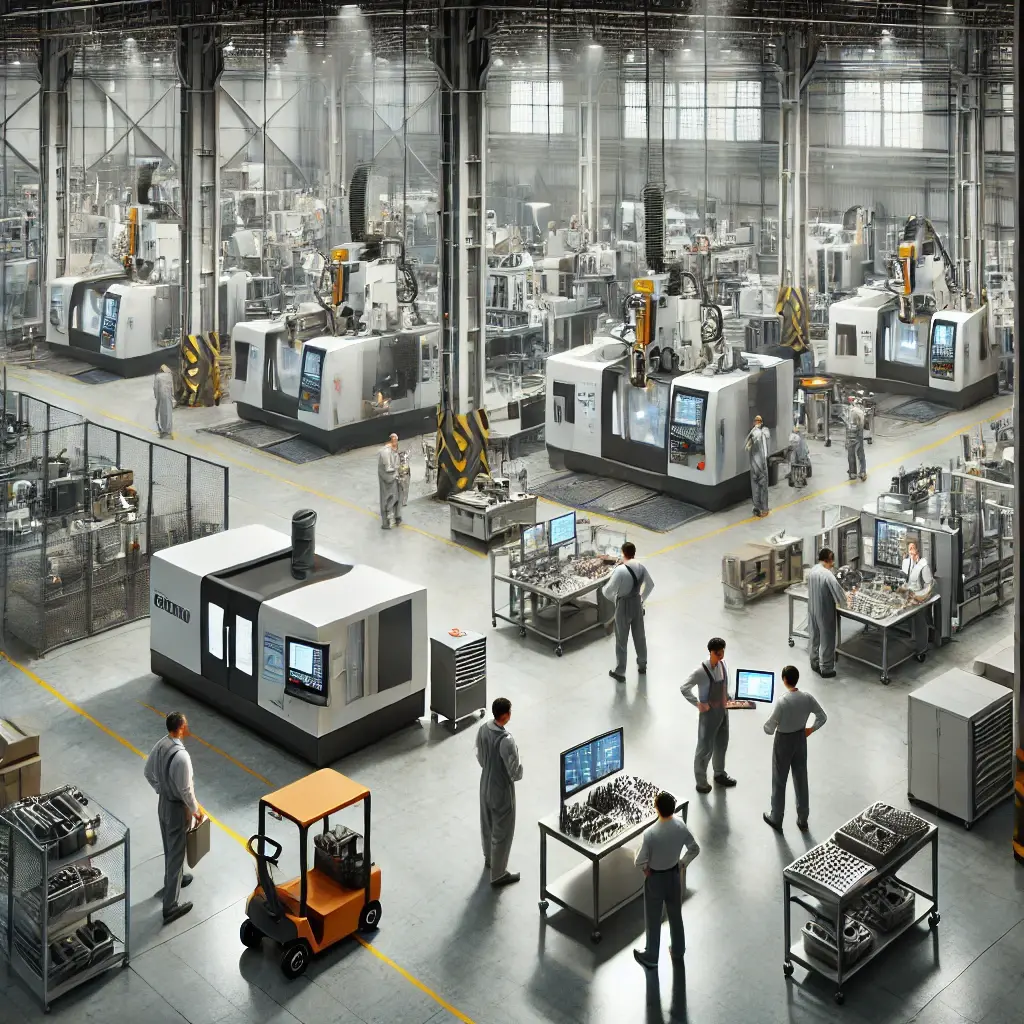
Strategies to Reduce Production Costs in Manufacturing
Introduction
Reducing production costs is a central objective for manufacturing companies looking to improve profitability while maintaining quality and competitiveness. Every cost item, from raw material procurement to equipment utilization, must be optimized to minimize losses and maximize productivity.
Efficiency depends on better production planning, strict cycle time management, and the integration of automation and real-time monitoring solutions.
In this article, we explore seven proven strategies to reduce manufacturing costs without sacrificing quality and performance.
Optimize Raw Material Management
Raw materials represent a significant share of manufacturing costs. To reduce these expenses, it's essential to optimize inventory management and procurement. Production planning software can anticipate material needs, avoid waste, and limit excess inventory that ties up capital.
Leveraging alternative suppliers, negotiating long-term purchase agreements, and using more economical materials without compromising quality are all effective levers. Some companies also implement recycling and reuse strategies for raw materials to limit costs and reduce their environmental footprint.
Improve Overall Equipment Effectiveness (OEE)
Overall Equipment Effectiveness (OEE) is a key indicator used to measure machine productivity and identify sources of loss. A machine monitoring system provides real-time visibility into availability, performance, and production quality.
A low OEE typically indicates frequent downtime, underused equipment, or high defect rates. To improve OEE, it's crucial to adopt preventive maintenance strategies, minimize unplanned downtime, and optimize manufacturing processes.
Automate and Digitize Processes
Automation plays a key role in reducing labor costs and increasing productivity. The integration of industrial robots, CNC machines, and digital control systems helps reduce human error and accelerate production rates.
Workforce planning software also facilitates resource management by avoiding work overload and underutilization. Live scheduling allows production to adjust to demand and enhances operational flexibility.
Reduce Waste and Improve Quality
Manufacturing defects, rework, and scrap increase production costs. Implementing real-time monitoring programs and using tools such as Six Sigma helps detect variability sources quickly and initiate corrective actions.
Stricter quality control and techniques like Just-in-Time manufacturing help minimize unnecessary inventory and improve production line efficiency. The goal is to produce with minimal waste while maintaining optimal quality.
Optimize Energy Consumption
Energy is a major cost factor in industry. Reducing energy use involves actions such as optimizing production cycles, using smart sensors to automatically adjust equipment consumption, and adopting more cost-effective energy sources.
Real-time energy monitoring can detect anomalies and identify the most energy-intensive machines. Improving facility insulation, using LED lighting, and implementing heat recovery systems are additional ways to reduce energy costs.
Reduce Changeover Times
Changeover times are a frequent source of productivity loss. Inefficient transitions between production batches lead to prolonged downtime and wasted resources. The SMED (Single-Minute Exchange of Die) method helps reduce these interruptions by optimizing changeover procedures.
A downtime tracking system helps analyze these interruptions and identify improvement levers. Standardizing procedures, training operators, and automating certain steps smooth the transition between batches and maximize available production time.
Optimize Workforce Management
Effective team management is key to reducing costs and avoiding inefficiencies. Workforce planning software helps better allocate tasks based on skills and production needs.
Live scheduling allows rapid response to demand fluctuations and resource adjustments. Continuous employee training and a collaborative work environment also help boost engagement and productivity.
Conclusion
Reducing production costs does not mean compromising on quality or performance. By implementing strategies such as raw material optimization, process automation, OEE improvement, and effective workforce planning, companies can increase profitability while maintaining high production levels.
Using machine monitoring systems, downtime tracking tools, and production planning software helps streamline operations and enhance flexibility. By applying these seven strategies, manufacturers can ensure better cost control and position themselves advantageously in an increasingly competitive market.