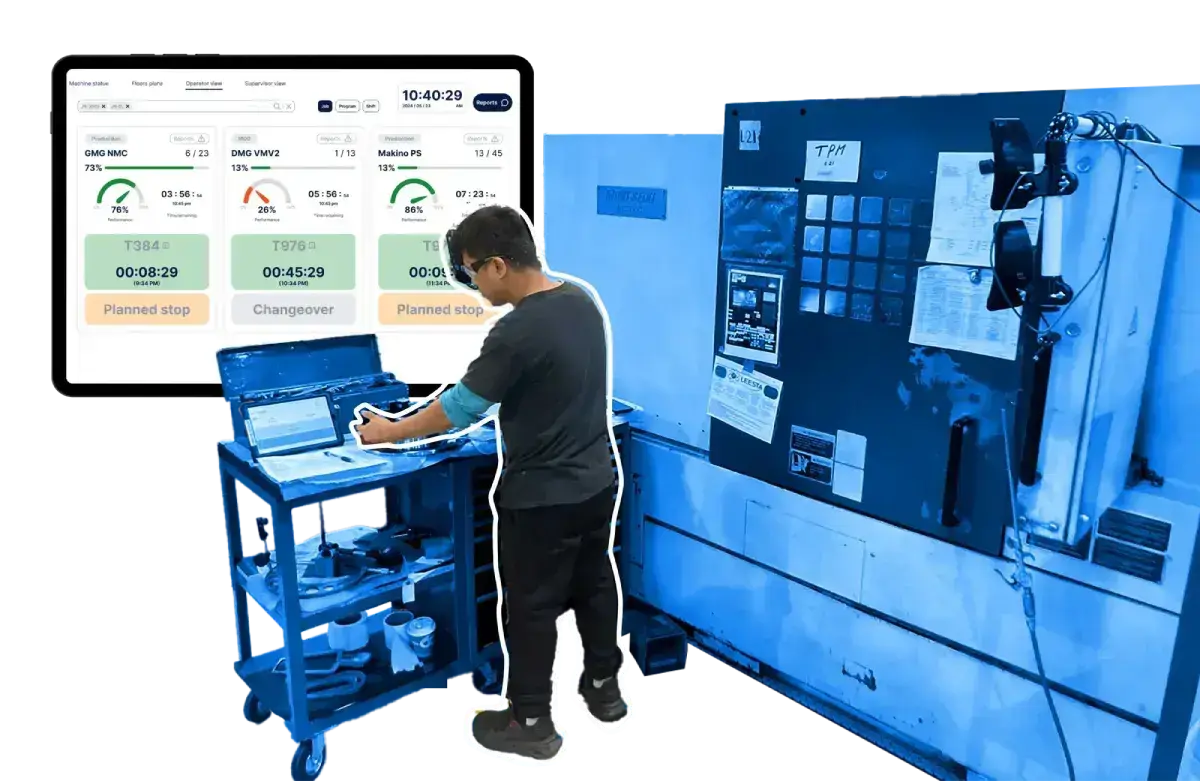
Le Travailleur Connecté dans l’Usinage CNC
Introduction
À l'ère de l'Industrie 4.0, la fabrication intelligente transforme le fonctionnement des usines en intégrant des technologies de pointe et des données en temps réel pour améliorer la productivité, la sécurité et la prise de décision. Au cœur de cette révolution se trouve le concept de travailleur connecté (Connected worker en anglais) — un terme qui désigne les employés équipés de technologies les reliant aux machines, aux données et aux autres membres de l'équipe en temps réel.
Mais que signifie réellement être un travailleur connecté, et pourquoi ce concept est-il essentiel pour l’avenir de la fabrication ? Dans cet article, nous expliquerons ce qui rend un travailleur — en particulier un machiniste ou un opérateur CNC — « connecté ». Nous examinerons les avantages et les défis, tout en fournissant des pistes pour aider les entreprises à adopter ces solutions dans leurs opérations.
L’évolution de la fabrication
La fabrication traditionnelle reposait principalement sur des processus manuels, où les opérateurs interagissaient peu avec les données. Les décisions étaient prises en fonction de l'expérience, de l'intuition et d'analyses postérieures. En revanche, la fabrication moderne repose sur des environnements pilotés par les données, où la connectivité des machines et l’automatisation jouent un rôle central. Le travailleur connecté représente une nouvelle étape de cette évolution, combinant les compétences humaines avec les données en temps réel issues des machines et des systèmes de production.
Les avantages des travailleurs connectés dans la fabrication intelligente
Communication avec les travailleurs
Le concept de Travailleur Connecté révolutionne la communication entre la gestion de la production et les travailleurs dans l'usinage CNC, favorisant clarté, efficacité et adaptabilité.
Voici comment :
- Communication fluide des affectations des opérateurs :
Des tableaux de bord connectés affichent les affectations des opérateurs directement au début d’un quart de travail, garantissant que les travailleurs savent exactement où aller et quelles machines opérer. Cela élimine toute confusion ou retard, les allocations étant directement liées au plan de production établi par le responsable. Un simple coup d'œil sur un écran ou des tablettes sur les machines offre une clarté immédiate sur les rôles à assumer.
Exemple : passer d’un tableau blanc manuel, long à mettre à jour, à un tableau d’affectation numérique basé sur la planification digitale.
2. Visibilité des tâches et opérations:
Les systèmes connectés permettent aux travailleurs de voir les tâches et opérations qui leur sont assignées, accompagnées d’instructions détaillées. Cette intégration entre la planification de la production et la visibilité de l’opérateur garantit que les travailleurs peuvent commencer leurs tâches rapidement, avec toutes les informations nécessaires accessibles en temps réel, réduisant ainsi les temps d'arrêt et améliorant l'efficacité des flux de travail.
Exemple : une vue sur la machine pour permettre à l’opérateur d’anticiper ses tâches.
-
Mises à jour en temps réel du plan :
Dans des environnements de production dynamiques, les plans peuvent changer en cours de quart en raison d'imprévus comme des pannes de machines ou des changements de priorités. Le concept de Travailleur Connecté garantit que les plans actualisés sont immédiatement communiqués via des tableaux de bord numériques. Les travailleurs ne dépendent plus de mises à jour verbales des superviseurs ; ils voient le nouveau plan instantanément, réduisant les malentendus et les temps d'arrêt. -
Boucle de retour en temps réel vers la planification :
Les systèmes connectés, alimentés par les données en temps réel des machines, suivent automatiquement la progression des tâches. Ce retour permet au système de planification de se mettre à jour en continu, reflétant l’état en direct des opérations. Les travailleurs, équipés de tablettes ou d’autres outils numériques, peuvent voir comment leurs tâches sont affectées et s’adapter en conséquence. Cette synchronisation entre les actions des travailleurs et la planification de la production assure un fonctionnement précis et agile de l’atelier.Le concept de l'ouvrier connecté dans l'usinage CNC : un pont entre gestion et efficacité
En comblant le fossé de communication entre la gestion de la production et les opérateurs, le concept de l’ouvrier connecté transforme les opérations d’usinage CNC. Non seulement il fournit aux opérateurs les informations nécessaires pour être performants, mais il garantit également que ces informations soient toujours exactes, à jour et accessibles. Cela se traduit par des flux de travail plus fluides, une adaptation plus rapide aux changements et une main-d'œuvre plus autonome et efficace.
Productivité et efficacité accrues
En accédant aux données en temps réel issues des machines, capteurs et systèmes de production, les ouvriers connectés prennent des décisions plus intelligentes sur le moment. Plutôt que d’attendre des rapports manuels ou des évaluations postérieures, les ouvriers connectés reçoivent des mises à jour en direct sur l’état des lignes de production, les performances des équipements et l’efficacité des flux de travail.
En identifiant rapidement les inefficacités ou les retards, ils peuvent ajuster leurs actions et résoudre les problèmes de manière proactive. Par exemple, si une machine accuse un retard dans son planning, les ouvriers reçoivent une alerte et peuvent réorganiser leur flux de travail pour réduire les temps morts ou rediriger les tâches vers des machines plus efficaces.
L’accès à des métriques de performance et des analyses permet également aux ouvriers de repérer des tendances et de proposer des améliorations. Ces optimisations réduisent les temps de cycle, améliorent l’utilisation des ressources et, au final, augmentent la production sans ressources supplémentaires.
Les données en direct permettent également aux ouvriers connectés de comprendre leur efficacité en temps réel, notamment par rapport aux objectifs de leur poste ou de leur quart de travail.
De meilleures prises de décisions pour la planification et l’ordonnancement
Les jours où l’intuition ou l’expérience suffisaient pour prendre des décisions en fabrication sont révolus. Les ouvriers connectés s’appuient sur des informations basées sur les données pour guider leurs actions et décisions, adoptant une approche plus scientifique dans la gestion de l’environnement de production.
Au lieu d’attendre que des managers ou des ingénieurs transmettent des informations, ils reçoivent un retour instantané sur le terrain. Par exemple, si une ressource précieuse est affectée à une machine pouvant fonctionner sans supervision jusqu’à la fin du quart, cela peut entraîner une perte de productivité. Grâce à des mises à jour en temps réel, les superviseurs peuvent rapidement visualiser cette information et réaffecter les ressources. L’ouvrier connecté verra ces changements immédiatement sur son tableau de bord, ce qui lui permettra de s’adapter rapidement.
En prenant en compte les charges de travail des opérateurs pour le reste du quart, les superviseurs peuvent réassigner les tâches pour équilibrer les charges, éviter les surcharges et exploiter au mieux les ressources sous-utilisées.
Les usines étant des environnements dynamiques où les conditions changent rapidement, les données issues des systèmes intégrés permettent aux superviseurs de prendre des décisions plus judicieuses et de s’aligner sur les objectifs globaux de l’entreprise.
Autonomisation et engagement des équipes
Doter les ouvriers d’une technologie améliorant leurs fonctions a un impact profond sur leur engagement et leur satisfaction au travail. Lorsqu’ils disposent des bons outils et des bonnes données, ils se sentent plus autonomes, motivés et capables de contribuer de manière significative au succès de l’organisation.
Prise en charge des responsabilités : Avec des données en temps réel et des analyses pertinentes, les ouvriers connectés peuvent assumer pleinement leurs responsabilités. Ils agissent de manière autonome et prennent des décisions qui reflètent leur expertise et les besoins du terrain. Ce niveau de contrôle favorise un sentiment de responsabilité et de fierté, améliorant le moral des équipes.
Apprentissage et développement continus : Dans un monde axé sur la technologie, les ouvriers sont plus engagés lorsqu’ils utilisent des outils modernes plutôt que des processus manuels obsolètes. Cela est particulièrement vrai pour les jeunes générations, désireuses d’acquérir de nouvelles compétences, de découvrir des technologies émergentes et de relever de nouveaux défis. En offrant ces opportunités, les entreprises renforcent une main-d’œuvre non seulement plus compétente, mais aussi plus fidèle, ce qui réduit le turnover.
Résolution proactive des problèmes : Les ouvriers connectés ne se contentent pas d’exécuter des tâches, ils identifient et résolvent des problèmes. Grâce aux analyses de données et à la connectivité des machines, ils disposent des outils nécessaires pour résoudre les problèmes de manière proactive, ce qui améliore les flux de travail, réduit les erreurs et favorise une culture d’amélioration continue.
Transparence et responsabilisation : En partageant les données de performance dans toute l’usine, les ouvriers connectés peuvent comparer leurs résultats à ceux de leurs collègues. Cela crée une transparence et un sentiment de responsabilité au sein des équipes. Cette saine compétition incite les travailleurs à rester motivés et à donner le meilleur d’eux-mêmes, renforçant l’efficacité globale de l’usine.
L’avenir des ouvriers connectés dans l’usinage CNC
À mesure que l’industrie adopte davantage l’automatisation, le rôle des ouvriers connectés évoluera. Les opérateurs collaboreront de plus en plus avec des machines et outils équipés d’intelligence artificielle, se concentrant sur la résolution de problèmes complexes et la prise de décisions tandis que les machines se chargeront des tâches répétitives. L’avenir de la fabrication intelligente repose sur une synergie entre l’ingéniosité humaine et la puissance technologique, avec les ouvriers connectés au cœur de cette évolution.
Conclusion
Le concept d’ouvrier connecté dans l’usinage CNC apporte des avantages significatifs qui transforment le fonctionnement des usines. En résumé, voici les principaux bénéfices:
- Communication avec les ouvriers : Des instructions claires et des mises à jour en temps réel garantissent que les opérateurs soient toujours informés et alignés avec les plans de production.
- Productivité et efficacité accrues : Les données en temps réel et les mises à jour fluides réduisent les temps morts et optimisent l’utilisation des ressources humaines et des machines.
- Meilleure prise de décision : Des données précises et en direct permettent aux superviseurs de mieux ajuster les plannings et les charges de travail.
- Autonomisation et engagement : Des outils modernes et des données transparentes motivent les opérateurs et les alignent sur les objectifs de l’usine.
Ces bénéfices créent un environnement de fabrication plus efficace, adaptatif et autonome, ouvrant la voie à une réussite à long terme.
La première étape pour exploiter la puissance de l’ouvrier connecté consiste à commencer à collecter des données depuis vos machines. Lancez-vous dès aujourd’hui avec l’offre gratuite de JITbase pour la collecte de données, valable pour 5 machines : Commencez maintenant