MANUFACTURING PRODUCTION PLANNING & WORKFORCE MANAGEMENT
100% of CNC machine shop production planning and daily operations is done using Excel.
We're about to change that with our Scheduling and Workforce Management system .
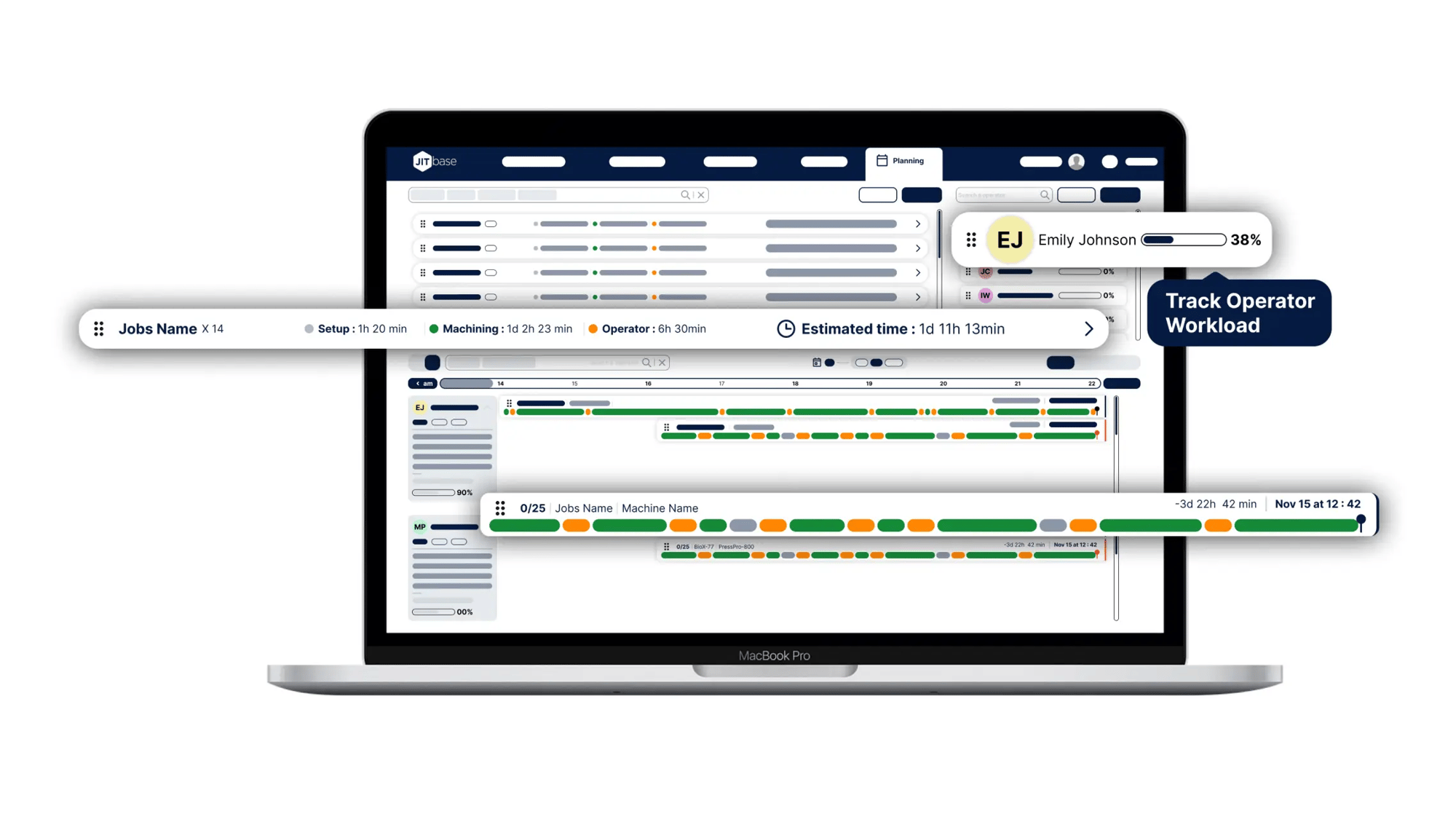
JITbase collects data on the workforce that no one else has
Unlike a traditional CNC Machine Monitoring System that track production metrics (OEE), JITbase exploits CNC machine data to address the machinist shortage and make the workforce 25% more efficient by feeding this data into our Production Management and Labour Management system (LMS).
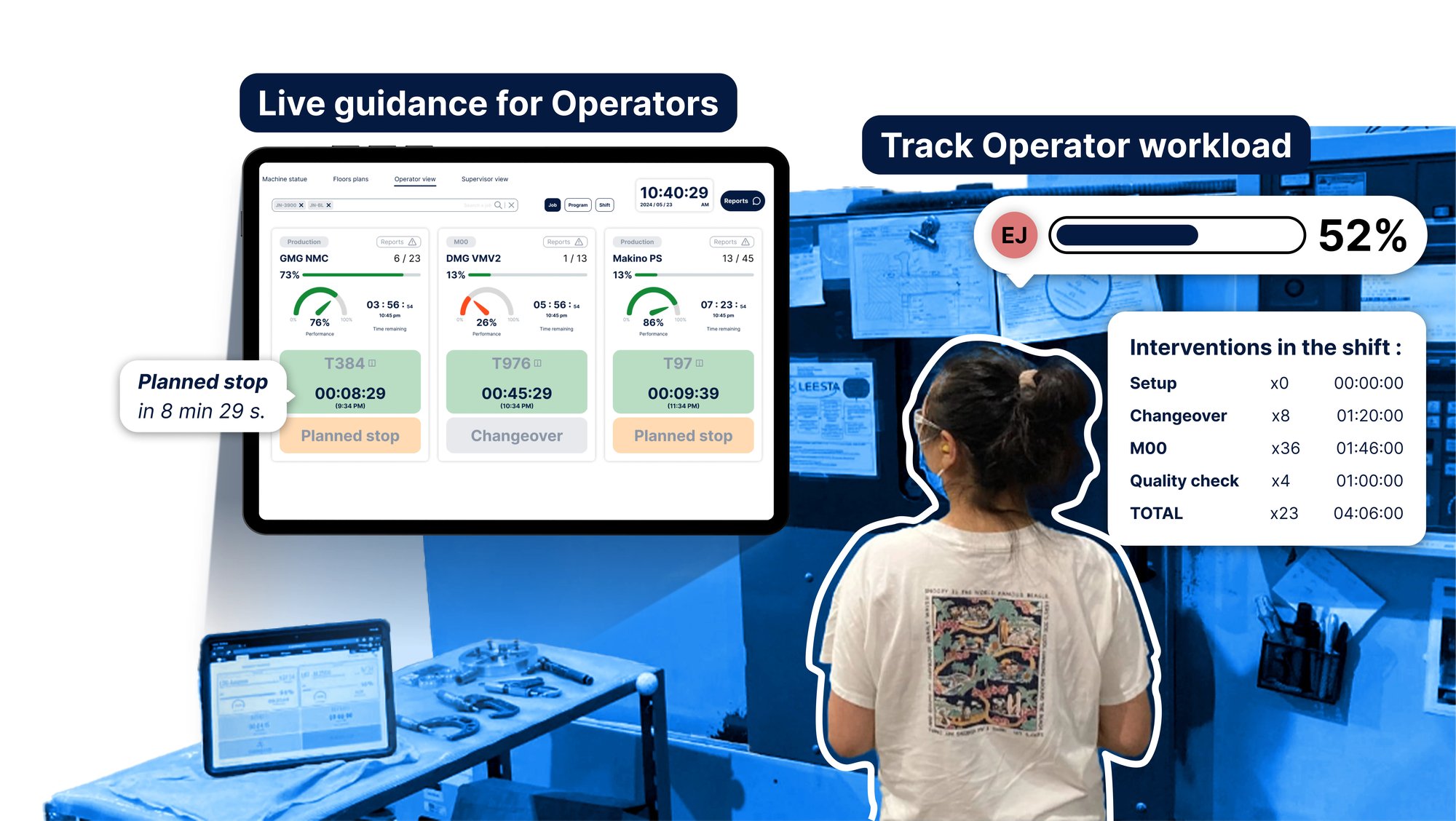
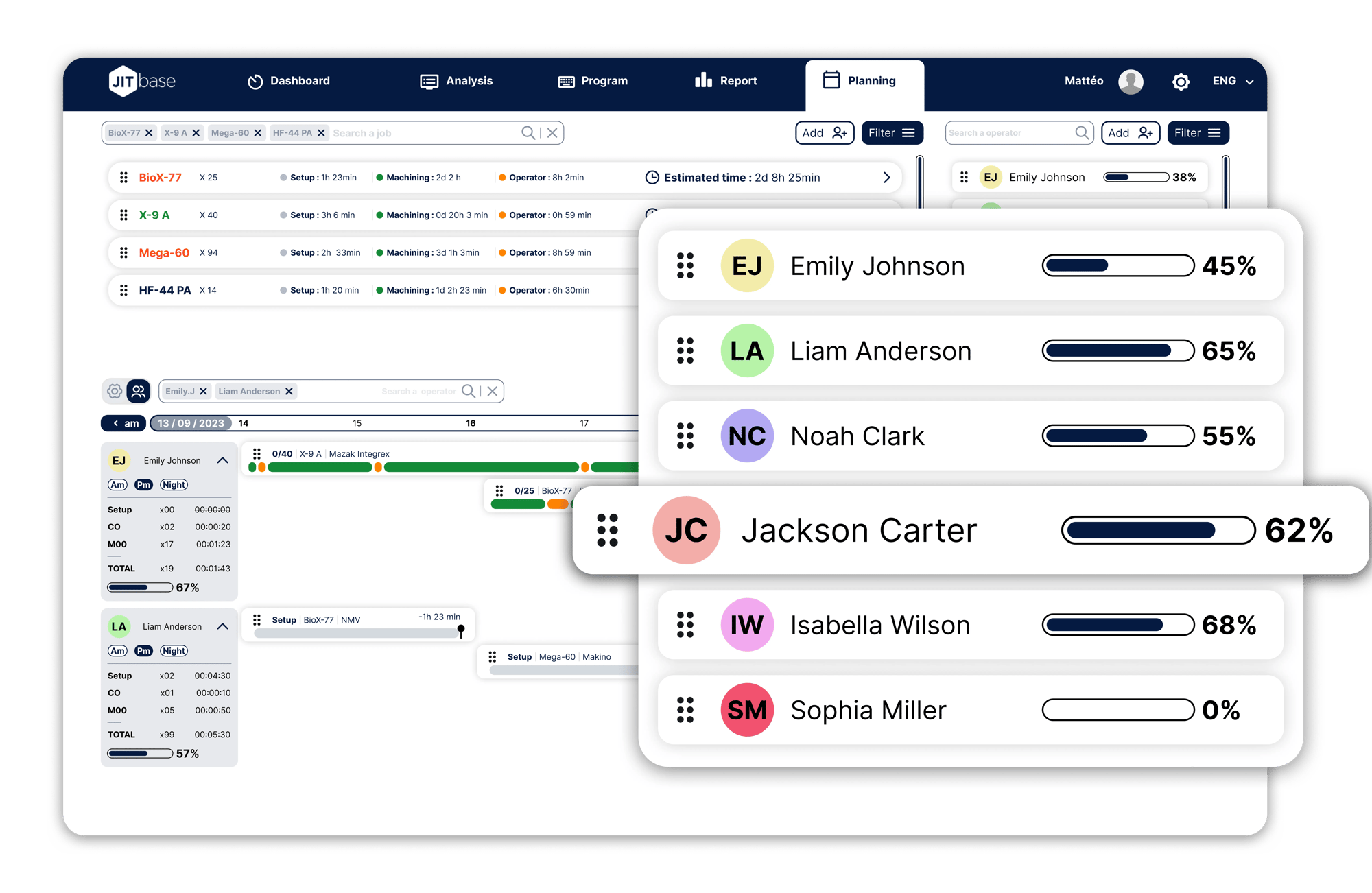
Human resource allocation thanks to Operator Workload
Is there a shortage of CNC machinists? Lack of human resources is the new bottleneck.
Instead of allocating operators on a limited number of machines next to one another, JITbase's Labour Management system (LMS) helps supervisors create a manufacturing production schedule and allocate operators based on their workload in the shift.
Operators manage more machines while being more efficient.
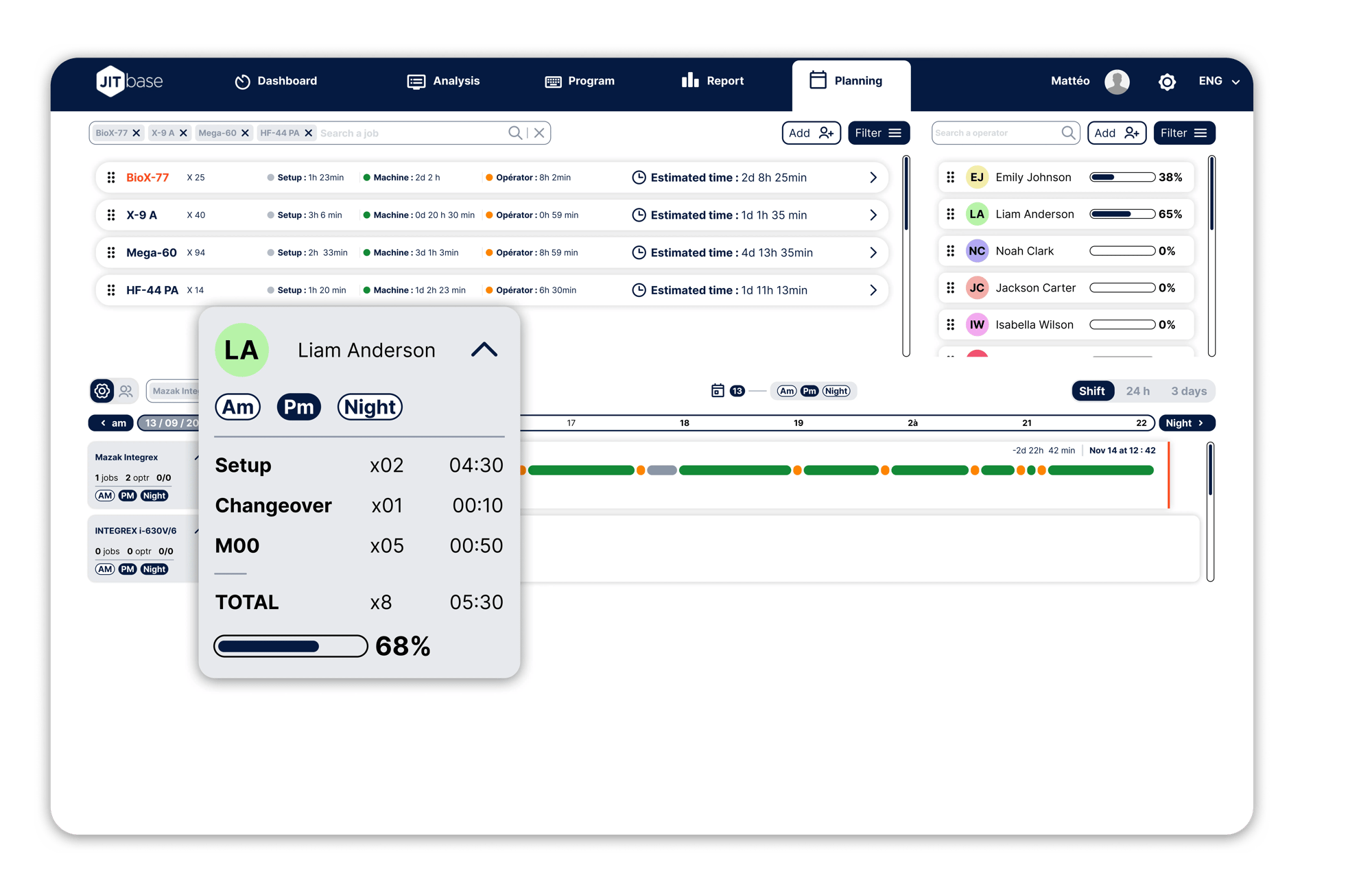
Advanced Workforce Planning and Production Scheduling
JITbase is also a WFM planning and scheduling software that takes the human factor into account by predicting the number of manual tasks in the shift: number of setups, number of part changeovers, number of M00, number of quality controls, etc.
Using a live planning tool, Supervisors can create and follow the manufacturing production schedule in real-time. They make informed decisions on operator allocation thanks to key information provided by JITbase.
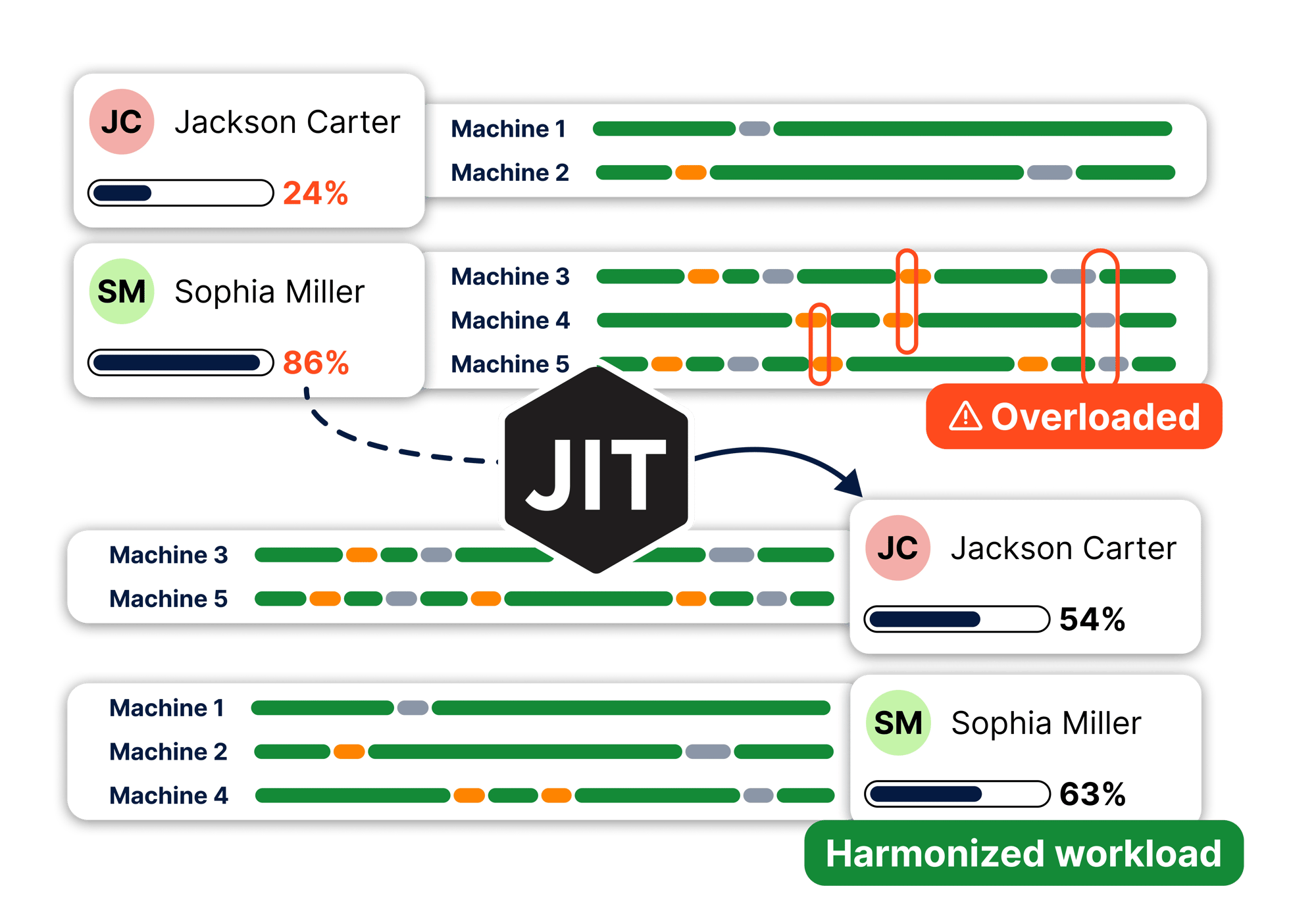
Harmonized workload for improved efficiency
Based on operator workloads, supervisors can better plan human resources on machines with our Labour Management system and live planning tool in order to maximize their efficiency.
JITbase helps:
- Find programs or jobs that can be managed together
- Detect overload situations that can impact performance
- Conversely, detect underload situations where an operator can manage more machines
The output is a harmonized workload among operators and more machines managed by a single operator.
JITbase is a complete CNC machine monitoring solution and advanced planning system that helps alleviate the machinist shortage.
Live Job and Work Order Tracking
JITbase ensures On Time Delivery (OTD) by using CNC machines monitoring and productivity, tracking the progress of work orders and by updating the Expected completion date in real-time.
It helps to:
- Plan and schedule production by knowing when each machine will be available
- Adjust the production plan if the Expected Completion time is not aligned with the deadline
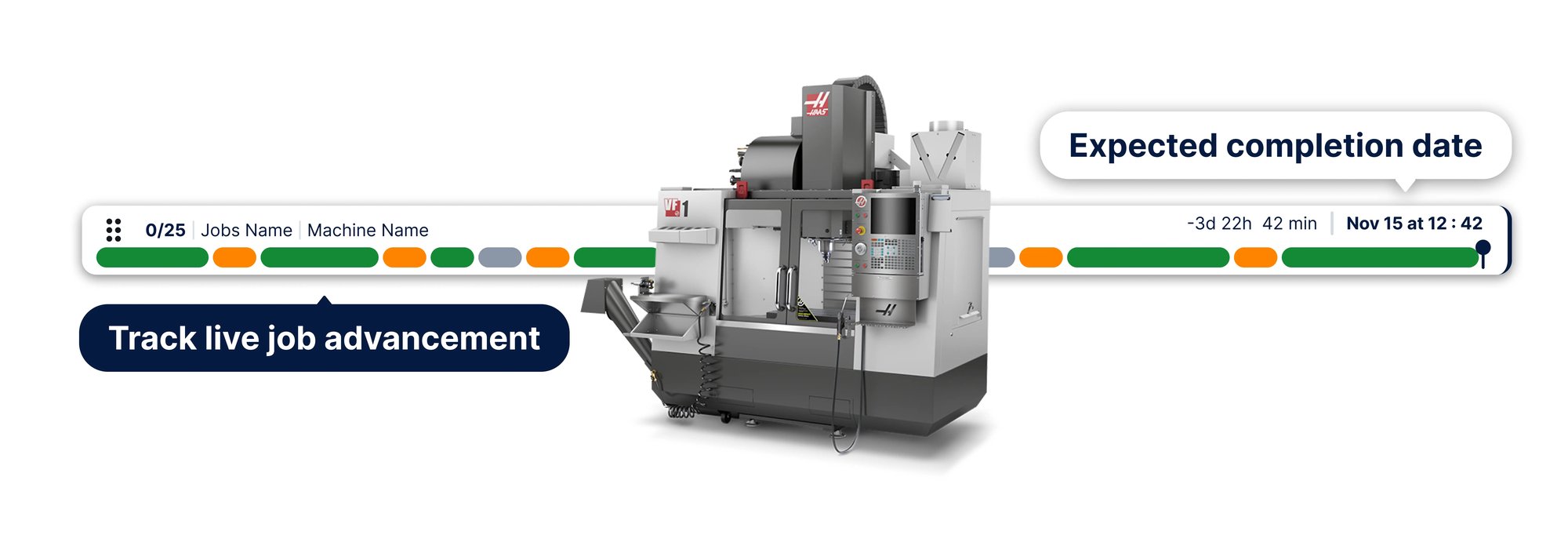
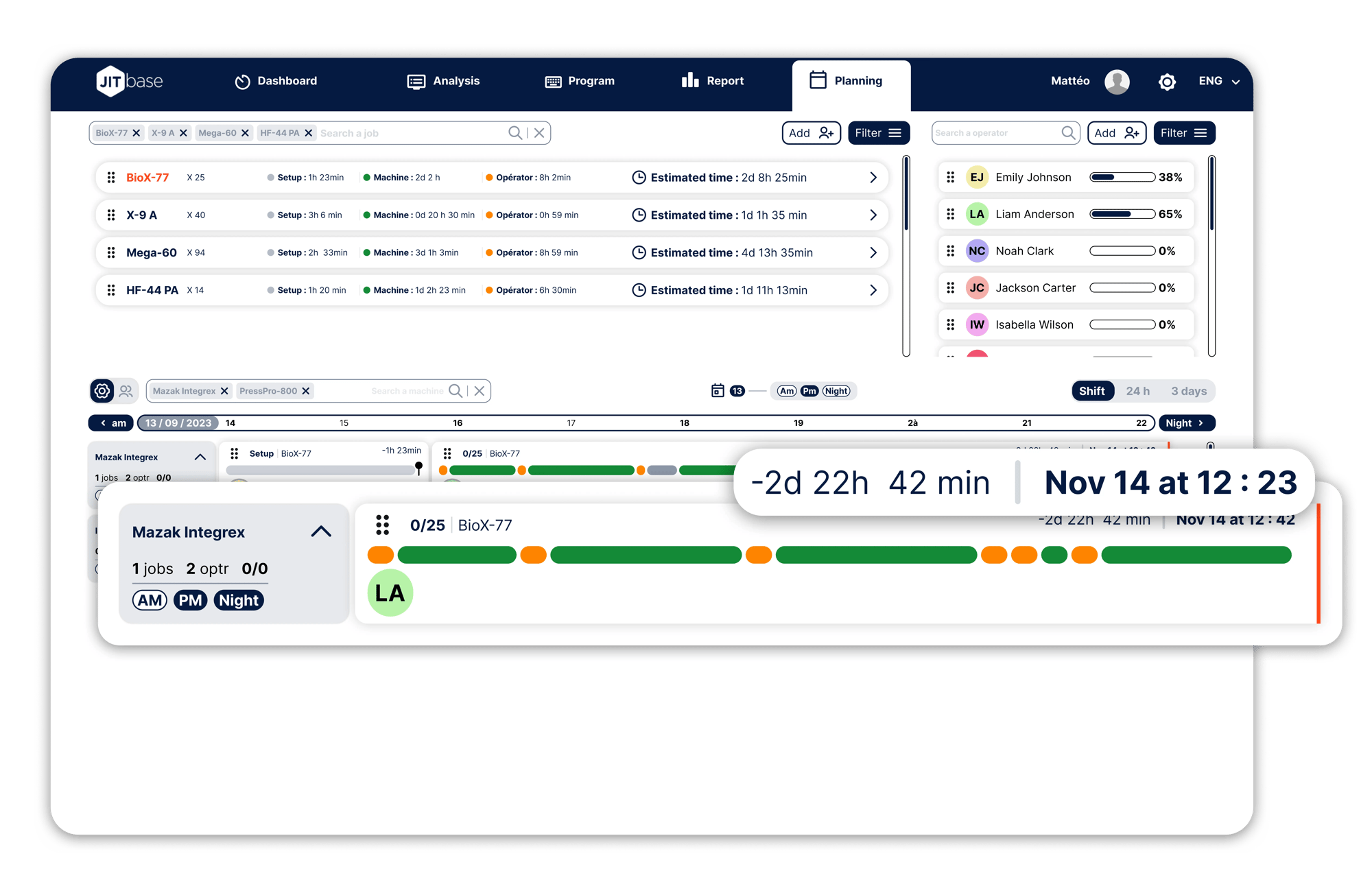
Production Planning and Scheduling
Based on live job progress and standard times thanks to CNC monitoring, JITbase predicts completion times.
Supervisors can play different scenarios such as opening/closing a shift, or assign overtime to ensure that deadlines are met.
In environments where priorities change rapidly due to constant new emergencies, JITbase designed an easy-to-use production planning system with drag-and-drop capabilities to help Supervisors adapt in real-time.
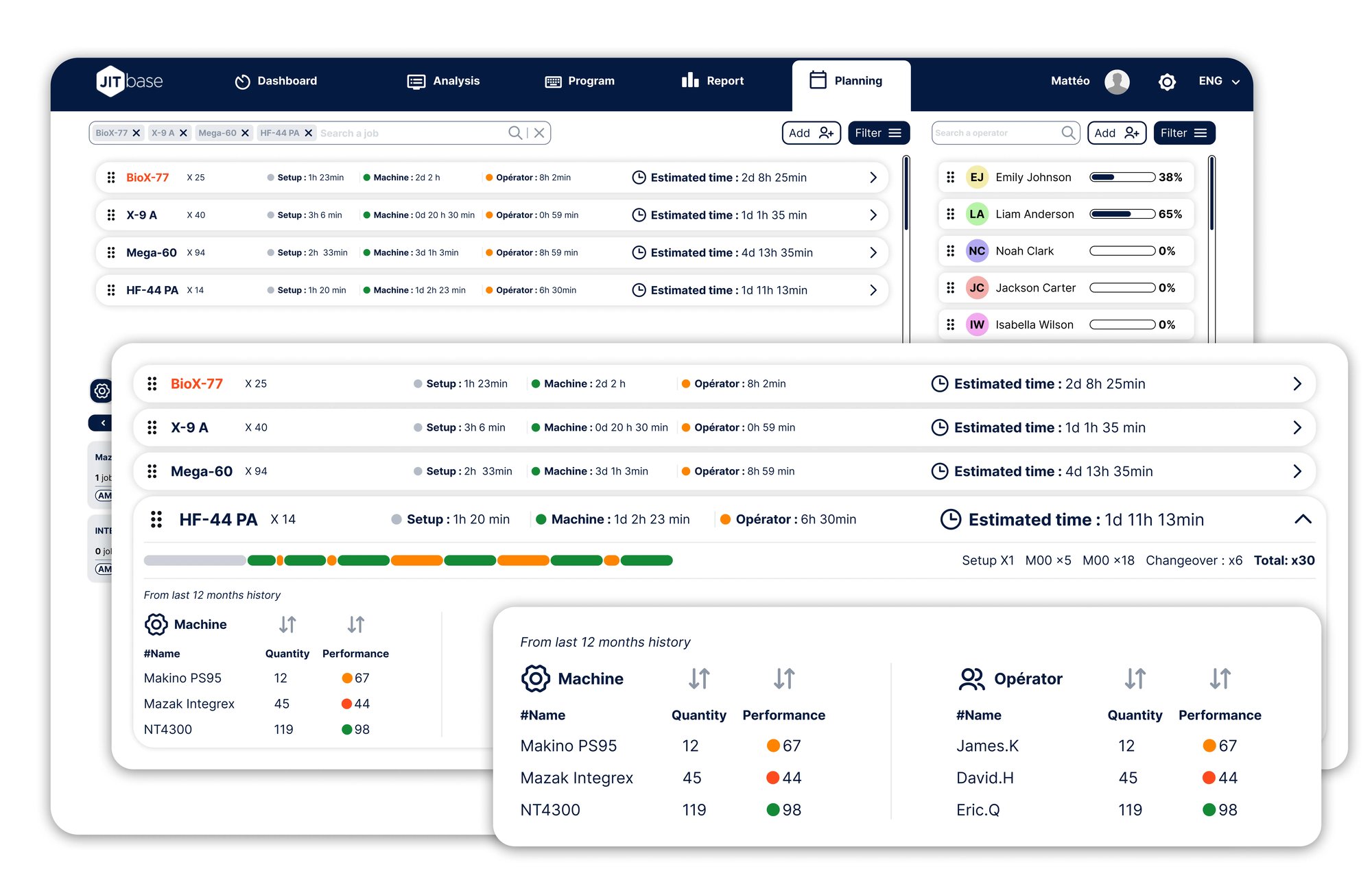
Gain key insights from past productions
Should you run the program on Machine A or Machine B? Which Operator should run it?
Using CNC Machine data collection, JITbase's production management software continuously learns from your productions to provide key insights.
Supervisors have access to past performances by machine and the information about which operator was in charge, which helps supervisors make better decisions in the production plan and operator allocation.
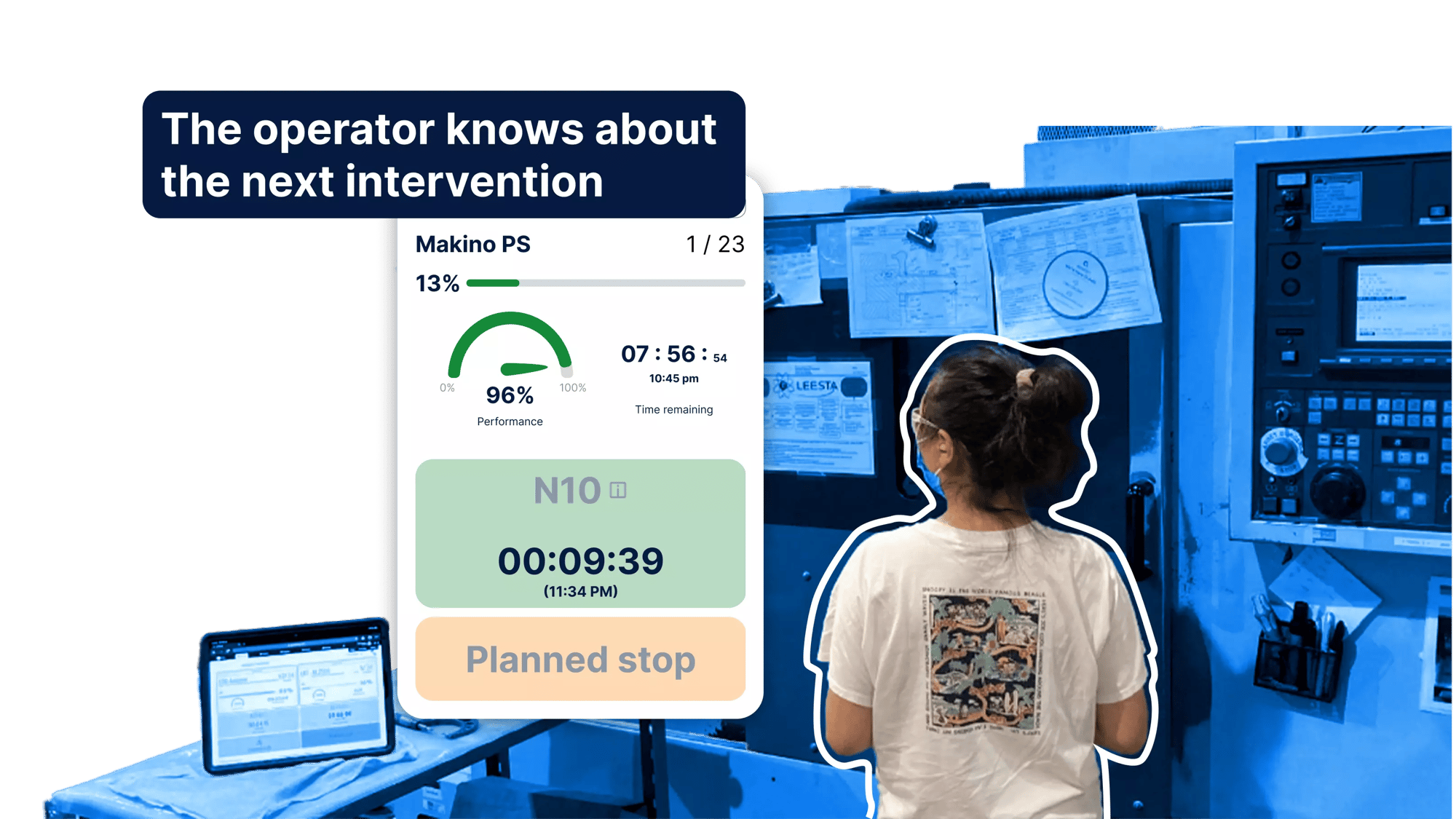
Live guidance for Operators
Thanks to our Workforce Planning and Manufacturing Scheduling tool, operators manage more machines. It becomes crucial to tell them when they are needed on each machine.
Tracking the program advancement in real time using CNC machine data collection, JITbase knows when the machine will reach the next stoppage. Adding a display on each machine, Operators can navigate from one CNC machine to the other, knowing when they are required for a manual intervention.
Being proactive not only makes them more efficient, it removes stress and makes their life easier all while minimizing the impacts of the machinist shortage.
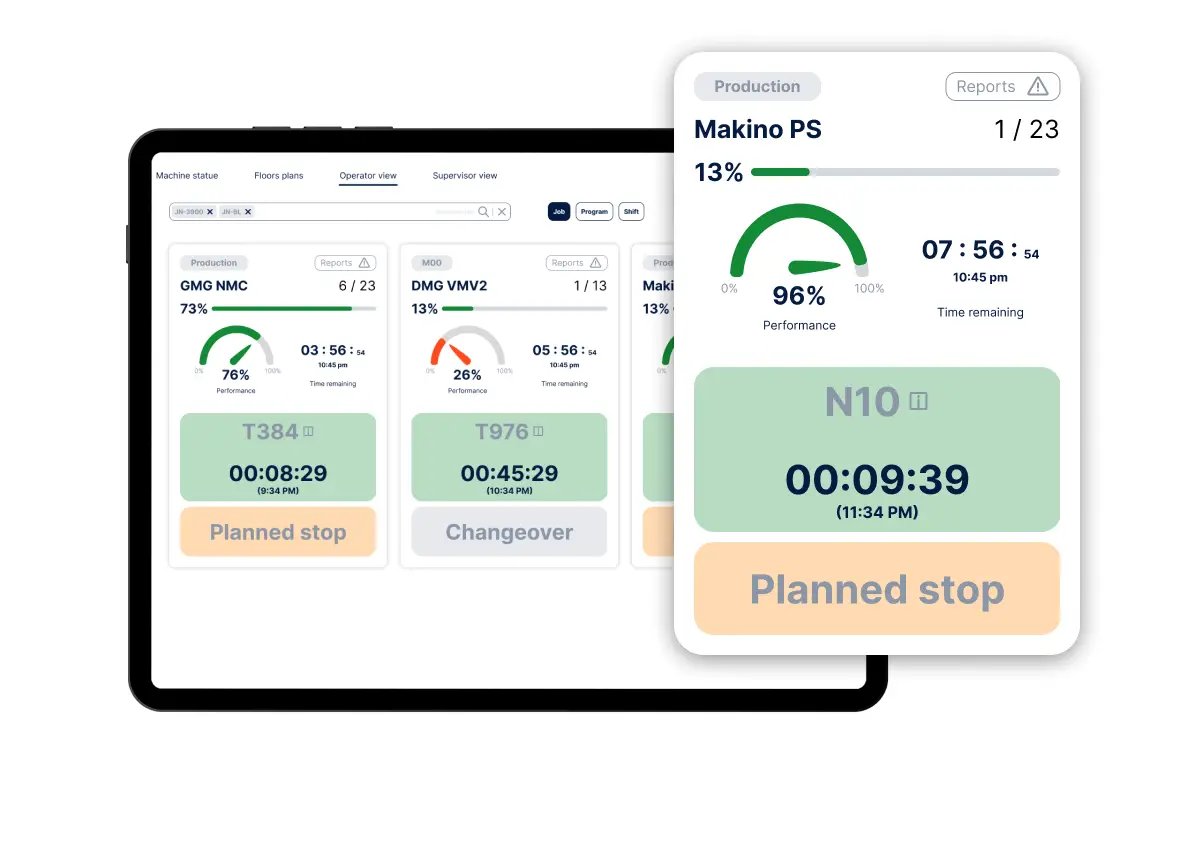
Live production KPIs for Supervisors
Unlike CNC Machine Monitoring Systems that only display live status and machine utilization (OEE), JITbase tracks:
- Parts completed vs. Shift Objective
- Live shift progress in %
- Performance of the shift
- Remaining time to complete the Shift Objective (based on standard times)
With JITbase’s advanced CNC tracking capabilities supervisors understand at a glance whether the production is going well or if a corrective action needs to be taken.
Ready to improve production planning and scheduling and optimize workforce efficiency?
Book a time with one of our experts or use our self-serve environment to try our free CNC machine monitoring software today.