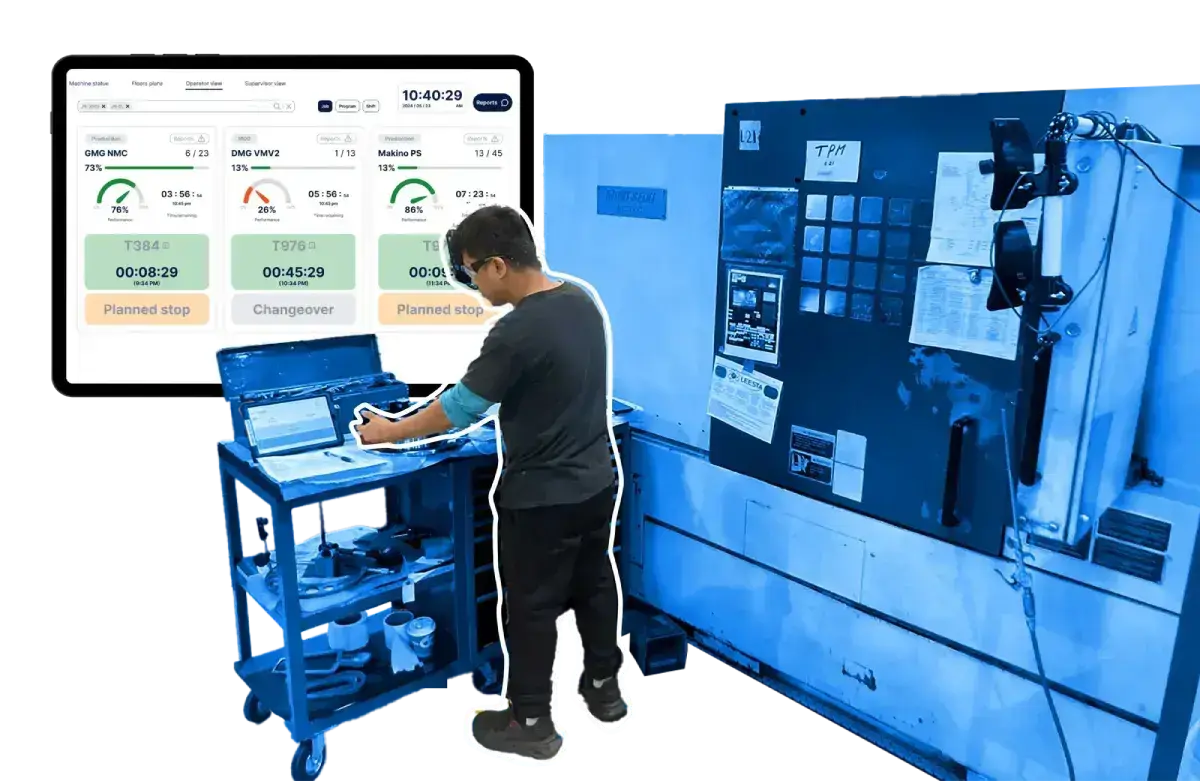
The Connected Worker in CNC Machining
Introduction
In the age of Industry 4.0, smart manufacturing is transforming the way factories operate, integrating cutting-edge technology and real-time data to improve productivity, safety, and decision-making. At the heart of this revolution is the “connected worker” — a term that refers to employees who are equipped with technology that connects them to machines, data, and each other in real time.
But what does it really mean to be a connected worker, and why is this concept so vital to the future of manufacturing? In this blog post, we will break down what makes a worker - specifically a machinist or a CNC operator - “connected”. We will explore the benefits and challenges, and provide insight into how companies can implement these solutions in their own operations.
The Evolution of Manufacturing
Traditional manufacturing relied heavily on manual processes, where operators had little interaction with data. Decisions were made based on experience, intuition, and after-the-fact analysis. In contrast, modern manufacturing is a data-driven environment where machine connectivity and automation play a central role. The connected worker represents a new frontier in this evolution—combining human skill with real-time data from machines and production systems.
Benefits of Connected Workers in Smart Manufacturing
Communication to the Worker
The Connected Worker concept revolutionizes communication between production management and workers in CNC machining, fostering clarity, efficiency, and adaptability.
Here’s how:
Seamless Operator Allocation Communication:
Connected dashboards display operator assignments directly at the start of a shift, ensuring workers know exactly where to go and which machines to operate. This eliminates confusion and delays, as allocation is clearly tied to the production plan set by the manager. A simple glance at a TV dashboard or tablets on the machines provides the worker with immediate clarity on their role for the day.
From manual time-consuming white board to update…
…to live allocation dashboard based on digital planning
Task and Operation Visibility:
Connected systems allow workers to view the specific jobs and operations they are assigned to, alongside detailed instructions. This integration between production planning and operator visibility ensures that workers can start their tasks promptly, with all the necessary information accessible in real-time, minimizing idle time and improving workflow efficiency.
On-machine operator view allowing workers to proactively see what they have to do
Real-Time Plan Updates:
In dynamic production environments, plans can change mid-shift due to unexpected events like machine downtimes or priority shifts. The Connected Worker concept ensures that updated plans are immediately communicated through digital dashboards. Workers no longer need to rely on supervisors for verbal updates; they see the new plan instantly, reducing miscommunication and downtime.
Live Feedback Loop to Planning:
Connected systems powered by real-time machine data track job progress automatically. This feedback allows the planning system to refresh continuously, reflecting the live status of operations. Workers, equipped with tablets or other digital tools, can see how their tasks are affected and adapt accordingly. This synchronized loop between worker actions and production planning ensures that the shop floor operates with precision and agility.
By bridging the communication gap between production management and workers, the Connected Worker concept transforms CNC machining operations. It not only provides workers with the information they need to perform effectively but also ensures that this information is always accurate, up-to-date, and accessible. This results in smoother workflows, faster adaptation to changes, and a more empowered and efficient workforce.
Enhanced Productivity and Efficiency
Have access to real-time data from machines, sensors, and production systems, Connected Workers make smarter decisions on the fly. Instead of waiting for manual reports or after-the-fact performance reviews, connected workers receive live updates on the status of production lines, equipment performance, and workflow efficiency.
By quickly identifying inefficiencies or delays in production, Connected Worker can adjust and solve problems in a more proactive manner. For example, if a specific machine is beyond schedule, workers are alerted and can adjust their workflow to reduce downtime or reroute tasks to more efficient machines.
With access to performance metrics and analytics, workers can spot trends and make suggestions for process improvements. These optimizations can lead to reduced cycle times, better resource utilization, and ultimately, greater output from the same resources.
Live metrics helps the Connected Worker to understand the live efficiency, including how they perform in regards to the shift objective
Better Decision-Making for planning and scheduling
The days of relying on intuition or experience alone to make decisions in manufacturing are fading. Connected workers use data-driven insights to guide their actions and decisions, providing a more scientific approach to managing the production environment.
Instead of waiting for managers or engineers to relay information, connected workers get instant feedback on the factory floor. For example, depending on the production advancement, a high-value resource may be allocated to a machine which can run without supervision for the remaining time of the shift, resulting in a loss of productivity from that resource. Thanks to live update information, Supervisors can quickly visualize this information and reallocate resources accordingly. The Connected Worker will see the information on his dashboard right away, given her the ability to adjust rapidly.
An example of operator workloads for the remainder of the shift. This provides supervisors with the opportunity to reassign workers and tasks, balancing workloads to prevent overloading and ensuring underutilized resources are utilized more effectively.
Factories are dynamic environments where conditions can change rapidly. Data from integrated systems allows supervisors to make better decisions by understanding operator workloads in the shift making production more efficient and streamlined.
Supervisors can rely on historical data to make decisions informed by trends. This removes the guesswork, making every choice more strategic and ensuring operations align with larger business goals.
Workforce Empowerment and Engagement
Equipping workers with technology that enhances their roles has a profound effect on engagement and job satisfaction. When workers have access to the right tools and data, they feel more empowered, motivated, and capable of making meaningful contributions to the success of the organization.
- Ownership of roles: When connected workers have access to real-time data and insights, they can take full ownership of their responsibilities. They can act with autonomy and make decisions that align with their expertise and the needs of the factory floor. This level of control fosters a sense of responsibility and pride in their work, boosting morale.
- Continuous learning and development: In a technology-driven world, connected workers are more likely to stay engaged when equipped with modern tools instead of outdated, inefficient manual processes. This is particularly true for younger generations, who are eager to upskill, explore emerging technologies, and embrace new challenges. By providing these opportunities, companies can foster a workforce that is not only more skilled but also more loyal, ultimately reducing employee turnover.
- Empowering problem-solving: Connected workers aren’t just executing tasks—they are identifying and solving problems. Through data insights and machine connectivity, they have the tools to proactively address issues, leading to improved workflows, fewer errors, and a culture that values continuous improvement.
- Transparency and Accountability: Sharing performance data across the factory allows Connected Workers to see how their performance compares to that of their colleagues. This fosters transparency and a sense of accountability among the workforce. The healthy competition that arises encourages workers to stay motivated and perform at their best, ultimately enhancing the overall efficiency of the factory.
Machine utilization data shared across the factory enables the Connected Worker to compare her performance with that of her colleagues.
These expanded points illustrate how connected workers benefit from technology, making manufacturing environments more productive, safe, and engaging for the workforce.
The Future of the Connected Worker in CNC Machining
As manufacturing continues to embrace automation, the role of the connected worker will evolve. Human workers will increasingly collaborate with AI-powered machines and tools, handling complex problem-solving and decision-making while machines take care of repetitive tasks. The future of smart manufacturing lies in a synergistic relationship between human ingenuity and technological prowess, with connected workers at the forefront.
Conclusion
The Connected Worker concept in CNC machining brings significant advantages that transform how factories operate. Here’s a summary of the key benefits:
- Communication to the Worker: Clear, real-time communication of tasks, machine allocation, and updates ensures workers are always informed and aligned with production plans.
- Enhanced Productivity and Efficiency: Real-time data and seamless updates reduce downtime and optimize the use of both human and machine resources.
- Better Decision-Making for Planning and Scheduling: Supervisors gain access to accurate, live data, enabling smarter adjustments to schedules and workloads throughout the shift.
- Workforce Empowerment and Engagement: Providing modern tools and transparent performance data keeps workers motivated, engaged, and aligned with factory goals.
These benefits collectively create a more efficient, adaptive, and empowered manufacturing environment, setting the stage for long-term success.
By addressing these critical aspects, JITbase helps manufacturers unlock the full potential of the Connected Workers in CNC machining, driving greater productivity and operational efficiency in smart manufacturing environments.
The first step to unlock the power of the Connected Worker is to start collecting data from your machines. Start now with JITbase offering allowing machine data collection for free up to 5 machines.